Bond Aluminium To Aluminium
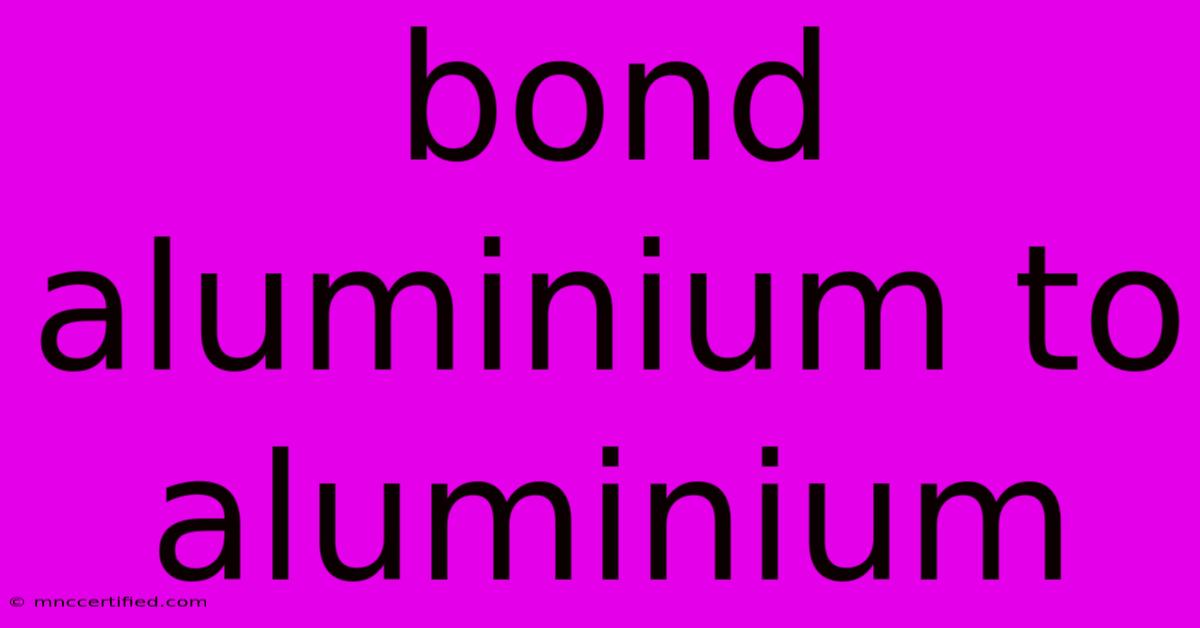
Table of Contents
Bonding Aluminum to Aluminum: A Comprehensive Guide
Aluminum's lightweight yet strong nature makes it a popular choice in various industries. However, joining aluminum pieces requires specific techniques to ensure a strong, durable bond. This comprehensive guide explores various methods for bonding aluminum to aluminum, focusing on the best practices for achieving optimal results. We'll cover everything from choosing the right adhesive to prepping the surface for a lasting bond.
Why Bond Aluminum to Aluminum?
Aluminum's versatility extends to its ability to be joined in numerous ways, creating intricate designs and robust structures. Bonding, as opposed to welding or riveting, offers several key advantages:
- No heat distortion: Welding can warp or distort delicate aluminum components. Bonding avoids this issue, preserving the integrity of the parts.
- Versatility: Bonding allows for joining pieces of varying shapes and sizes, even those with intricate designs.
- Cost-effectiveness: In many cases, bonding is a more economical solution than other joining methods, especially for small-scale projects or intricate designs.
- Corrosion resistance: A properly executed bond maintains the aluminum's inherent corrosion resistance.
Methods for Bonding Aluminum to Aluminum
Several methods effectively bond aluminum to aluminum. The best choice depends on factors like the application's demands, the materials' thickness, and the required bond strength.
1. Adhesives: A Popular Choice
Adhesives are a widely used and highly effective method for bonding aluminum to aluminum. Several types offer excellent adhesion and durability:
- Epoxy Adhesives: These two-part adhesives are known for their high strength, excellent chemical resistance, and versatility. They are suitable for a wide range of applications and offer good gap-filling capabilities. Keyword: Epoxy Aluminum Bonding
- Acrylic Adhesives: Acrylic adhesives offer fast curing times and good strength, making them suitable for many applications. They are often chosen for their ease of use and lower cost compared to epoxies. Keyword: Acrylic Aluminum Adhesive
- Cyanoacrylate (Super Glue): While quick-setting and convenient, cyanoacrylate adhesives generally offer lower strength compared to epoxies or acrylics. They are best suited for smaller, less demanding projects. Keyword: Super Glue Aluminum
Choosing the right adhesive: Consider the strength requirements, the gap between the surfaces, the environmental conditions, and the curing time needed when selecting an adhesive. Always follow the manufacturer's instructions carefully.
2. Mechanical Fasteners: A Supplementary Approach
Mechanical fasteners like rivets, screws, and bolts can supplement adhesive bonding, especially for high-stress applications. This combined approach offers superior strength and durability. However, remember that drilling holes weakens the aluminum. Keyword: Aluminum Riveting
3. Welding: For High-Strength Applications
While welding offers exceptional strength, it requires specialized equipment and expertise. It’s also more prone to causing heat distortion. This method is usually reserved for high-strength applications where the potential for distortion is less of a concern. Keyword: Aluminum Welding
Preparing the Aluminum Surfaces: Key to Success
Proper surface preparation is crucial for achieving a strong and lasting bond. This involves:
- Cleaning: Remove all dirt, grease, oil, and other contaminants using a suitable solvent. Acetone or isopropyl alcohol are commonly used.
- Deburring: Remove any burrs or sharp edges that might hinder proper adhesion.
- Surface Roughening: Increasing the surface area by slightly roughening the aluminum improves the adhesive's mechanical grip. This can be done using abrasive blasting, sanding, or chemical etching. Keyword: Aluminum Surface Preparation
Optimizing Your Bond
- Proper Adhesive Application: Follow the manufacturer's instructions carefully regarding the amount of adhesive to use and the application technique.
- Clamping: Applying appropriate clamping pressure during curing ensures a strong bond by preventing air gaps and maintaining consistent contact between surfaces.
- Curing Time: Allow sufficient curing time for the adhesive to reach its full strength. This varies depending on the adhesive type and environmental conditions.
Conclusion: Achieving a Strong Aluminum-to-Aluminum Bond
Bonding aluminum to aluminum is a viable and often preferred method for joining these lightweight yet strong materials. By understanding the various bonding methods, meticulously preparing the surfaces, and carefully following adhesive instructions, you can achieve a strong, durable, and long-lasting bond, suitable for a wide range of applications. Remember to always prioritize safety and wear appropriate personal protective equipment when working with adhesives and solvents.
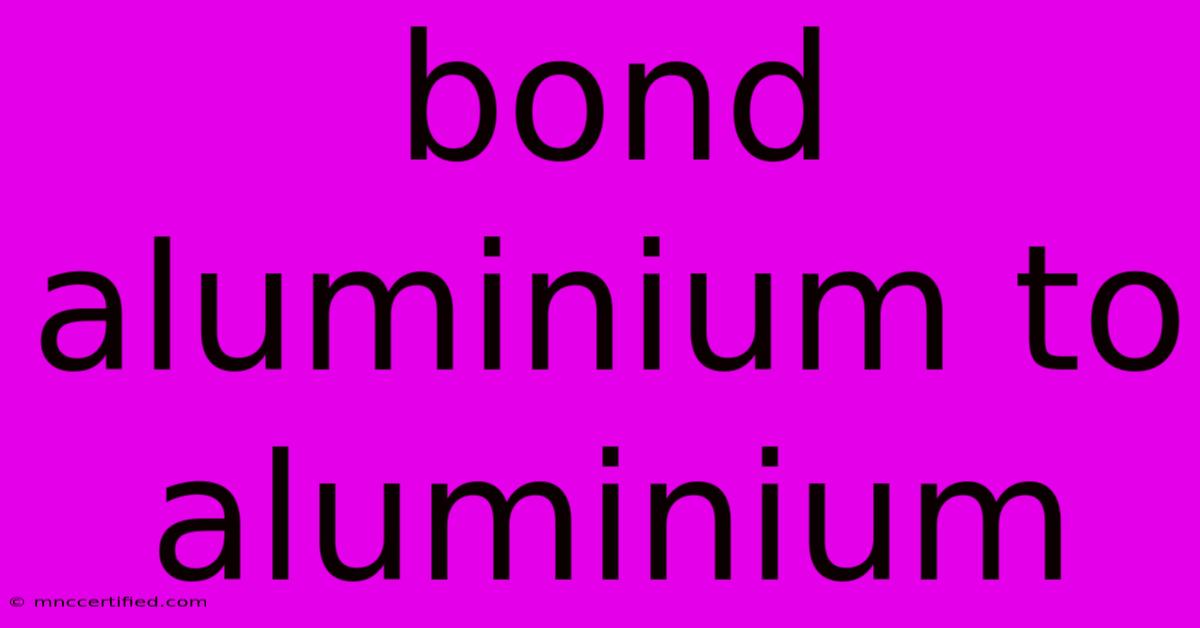
Thank you for visiting our website wich cover about Bond Aluminium To Aluminium. We hope the information provided has been useful to you. Feel free to contact us if you have any questions or need further assistance. See you next time and dont miss to bookmark.
Featured Posts
-
Home Insurance Fort Smith Ar
Dec 01, 2024
-
Insurance Jobs Birmingham Al
Dec 01, 2024
-
Football Game Missouri Vs Arkansas Updates
Dec 01, 2024
-
Forest Vs Ipswich Premier League Result
Dec 01, 2024
-
208 M Blazers Player To Lakers
Dec 01, 2024