Bonding Aluminium To Aluminium
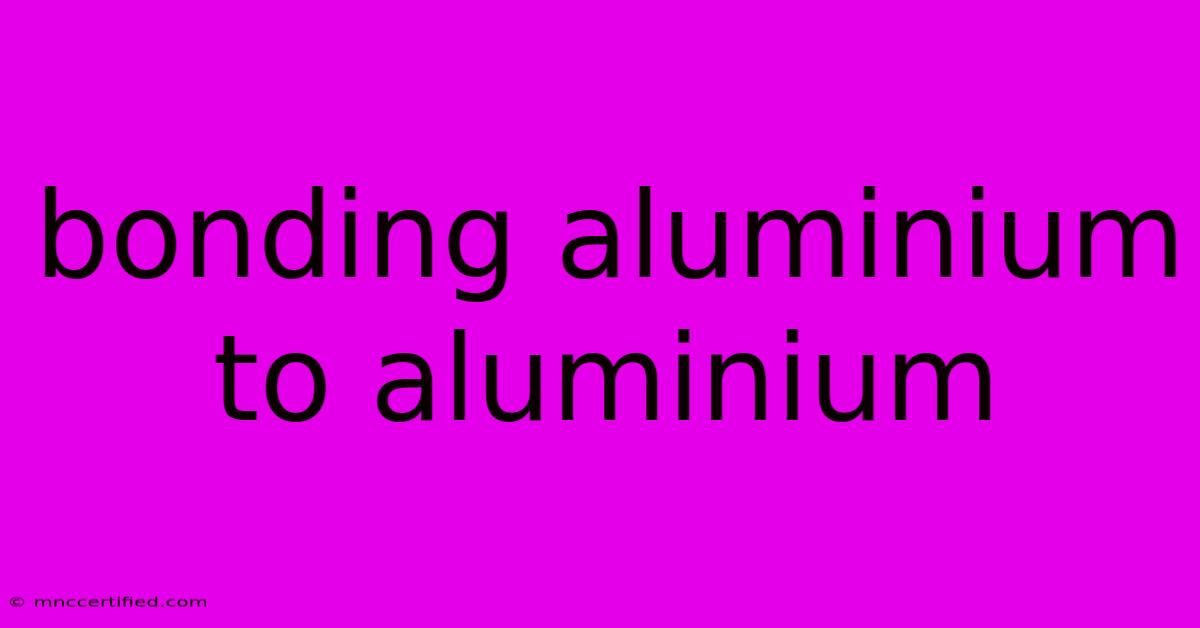
Table of Contents
Bonding Aluminum to Aluminum: A Comprehensive Guide
Aluminum's lightweight yet strong nature makes it a popular choice in various industries. However, joining aluminum components effectively requires specialized techniques. This comprehensive guide explores the most effective methods for bonding aluminum to aluminum, covering everything from choosing the right adhesive to ensuring a durable, long-lasting bond.
Understanding the Challenges of Aluminum Bonding
Aluminum presents unique challenges when it comes to bonding. Its surface is highly reactive, readily forming a thin oxide layer (aluminum oxide) that acts as a barrier, preventing good adhesion. This oxide layer must be properly addressed to achieve a strong, reliable bond. Furthermore, the metal's high thermal conductivity can affect the curing process of some adhesives.
Key Considerations Before Bonding:
- Surface Preparation: This is arguably the most crucial step. Impurities, oils, and the aluminum oxide layer significantly impact bond strength.
- Adhesive Selection: Different adhesives offer varying strengths, curing times, and temperature resistance. Choosing the right adhesive is paramount.
- Environmental Conditions: Temperature and humidity can influence the bonding process and the final bond strength.
Effective Methods for Bonding Aluminum to Aluminum
Several methods effectively join aluminum components. The best choice depends on factors like the application's demands (strength, temperature resistance, etc.), the size and shape of the components, and the available resources.
1. Adhesive Bonding: A Versatile Solution
Adhesive bonding offers a versatile and cost-effective solution for many aluminum-to-aluminum joining applications. However, proper surface preparation is essential for success.
Types of Adhesives Suitable for Aluminum:
- Epoxy Adhesives: A popular choice due to their high strength, versatility, and relatively easy application. Two-part epoxy systems are generally preferred for their superior strength. Look for epoxies specifically formulated for metals.
- Acrylic Adhesives: These offer excellent gap-filling properties and are suitable for less demanding applications. They are often faster curing than epoxies.
- Cyanoacrylate (Super Glue): While convenient for quick repairs, cyanoacrylates generally offer lower strength than epoxies. They are best suited for smaller, less critical bonds.
Surface Preparation for Adhesive Bonding:
- Cleaning: Thoroughly clean the aluminum surfaces with a suitable solvent (e.g., acetone or isopropyl alcohol) to remove oils, grease, and other contaminants.
- Deburring: Remove any burrs or sharp edges that could prevent proper adhesion.
- Abrasive Blasting or Mechanical Cleaning: For optimal results, consider abrasive blasting (e.g., with alumina or glass beads) or mechanical cleaning (e.g., wire brushing) to remove the aluminum oxide layer. This significantly improves surface roughness, leading to better mechanical interlocking with the adhesive.
2. Welding: High-Strength Joining
Welding provides the strongest bond for aluminum, ideal for high-stress applications. However, it requires specialized equipment and expertise. Common welding techniques for aluminum include:
- Gas Tungsten Arc Welding (GTAW) or TIG Welding: Produces high-quality welds with excellent control and minimal heat input.
- Gas Metal Arc Welding (GMAW) or MIG Welding: A faster process than TIG welding, but requires more skill to avoid porosity.
- Resistance Spot Welding: Suitable for joining sheet metal, producing strong localized welds.
3. Riveting: A Mechanical Joining Technique
Riveting is a mechanical fastening method suitable for joining aluminum sheets or components. While not technically bonding, it provides a strong and reliable connection.
4. Other Bonding Methods
Other less common methods include brazing and soldering. These methods require specialized skills and equipment.
Choosing the Right Method: A Decision Matrix
Method | Strength | Cost | Complexity | Speed | Heat Resistance |
---|---|---|---|---|---|
Adhesive Bonding | Moderate to High | Low to Moderate | Low to Moderate | Moderate to High | Varies by Adhesive |
Welding | Very High | Moderate to High | High | Low to Moderate | Very High |
Riveting | Moderate | Low | Low | Moderate | Moderate |
Maximizing Bond Strength and Durability
Regardless of the chosen bonding method, following these best practices will enhance the strength and longevity of the bond:
- Proper surface preparation is paramount. Don't skip this crucial step!
- Apply adhesive according to the manufacturer's instructions. This includes proper mixing ratios, curing times, and clamping pressure (if necessary).
- Control environmental conditions. Temperature and humidity can affect curing and bond strength.
- Use appropriate tooling and equipment. The right tools make a big difference in the quality of the bond.
By following these guidelines and selecting the appropriate method, you can achieve strong, reliable bonds for your aluminum components. Remember that careful planning and execution are key to successful aluminum-to-aluminum bonding.
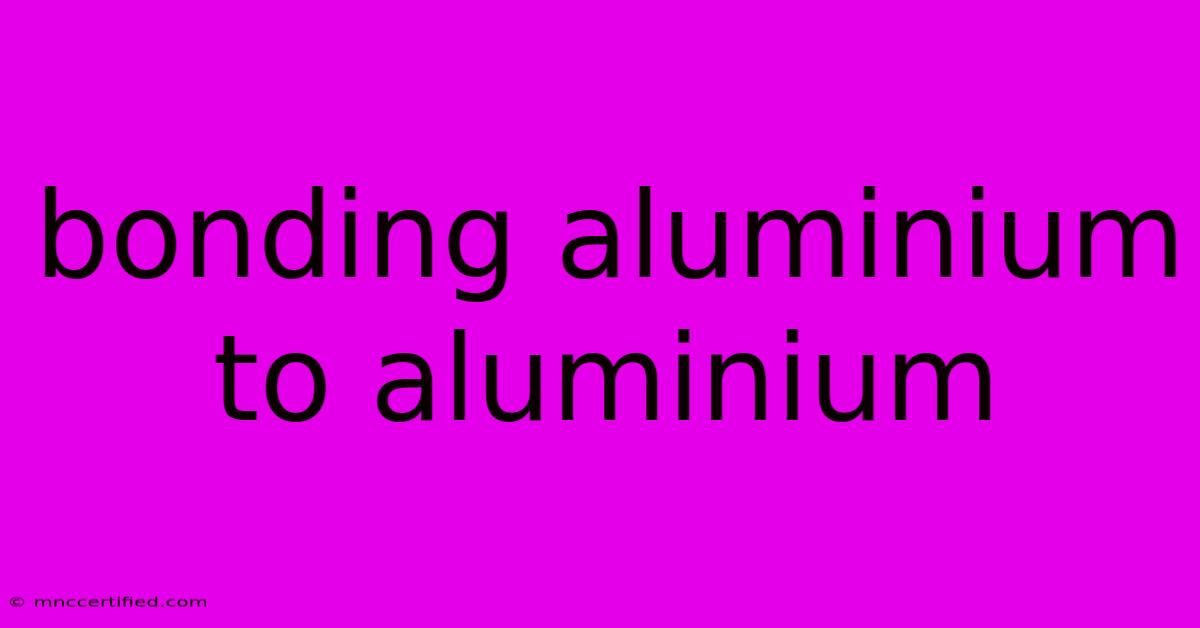
Thank you for visiting our website wich cover about Bonding Aluminium To Aluminium. We hope the information provided has been useful to you. Feel free to contact us if you have any questions or need further assistance. See you next time and dont miss to bookmark.
Featured Posts
-
Dear Santa Movie Review Hilarious
Nov 26, 2024
-
Press Conference And Free Throws Maui Photos
Nov 26, 2024
-
Sterling Life Insurance Company
Nov 26, 2024
-
Cayman Islands Investment Funds
Nov 26, 2024
-
Mc Conkey Injury News Game Status Update
Nov 26, 2024