Does Fiberglass Bond To Plastic
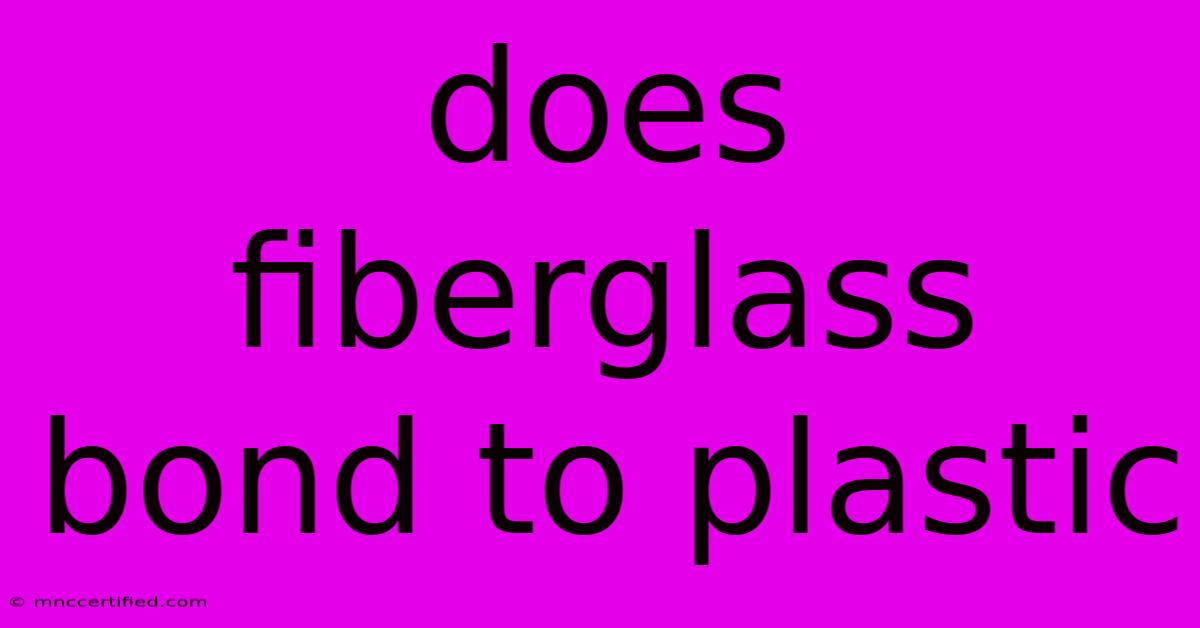
Table of Contents
Does Fiberglass Bond to Plastic? A Comprehensive Guide
Fiberglass and plastic are ubiquitous materials in countless applications, from automotive parts and boats to home insulation and electronics. A common question arises: does fiberglass bond to plastic? The short answer is: it depends. The success of bonding fiberglass to plastic hinges on several crucial factors, including the types of plastic and fiberglass, the surface preparation, and the adhesive used. This comprehensive guide will delve into these aspects, helping you understand the nuances and achieve successful bonding.
Understanding the Challenges: Why it's Not Always Easy
The challenge lies in the inherent differences between fiberglass and plastics. Fiberglass, a composite material of glass fibers bound together by a resin, possesses a relatively porous and rough surface. Plastics, on the other hand, can vary significantly in their surface properties. Some are smooth and non-porous, making adhesion difficult. Others may be slightly porous but still present challenges due to their chemical composition. Essentially, achieving a strong bond requires overcoming these surface discrepancies and finding a suitable adhesive with the right properties.
Types of Plastic: A Key Consideration
Not all plastics are created equal. The type of plastic significantly impacts the bonding process. Here’s a breakdown:
-
Thermoplastics (e.g., ABS, PVC, Polypropylene): These plastics soften when heated and can be remolded. Bonding thermoplastics requires careful surface preparation to ensure proper adhesion, often involving mechanical methods like sanding or chemical etching to increase surface roughness. Specific primers may also be necessary to improve the adhesive's hold.
-
Thermosets (e.g., Epoxy, Polyester): These plastics harden irreversibly after curing and are generally more difficult to bond to. Specialized adhesives and careful surface preparation are crucial for success.
-
Polyethylene (PE) and Polypropylene (PP): These are notoriously difficult plastics to bond to due to their low surface energy. They require aggressive surface treatments like plasma treatment or corona discharge to enhance adhesion.
Selecting the Right Adhesive: The Key to Success
The adhesive is the cornerstone of a successful bond. The choice depends heavily on the types of plastic and fiberglass involved, as well as the intended application. Common choices include:
-
Epoxy Resins: Known for their high strength and versatility, epoxy resins are a popular choice for bonding fiberglass to many plastics. They are often chosen for their excellent adhesion to a wide range of surfaces and their ability to withstand various environmental conditions.
-
Cyanoacrylate (Super Glue): While quick and easy to use, super glue's bonding strength may be insufficient for demanding applications. It's best suited for smaller, less stressed joints.
-
Specialty Adhesives: For challenging plastics like polyethylene and polypropylene, specialized adhesives designed for low-surface-energy materials are often necessary. These may involve primers or surface activators to promote adhesion.
Surface Preparation: The Often-Overlooked Crucial Step
Regardless of the adhesive chosen, proper surface preparation is paramount. This involves:
-
Cleaning: Thoroughly clean both the fiberglass and plastic surfaces using a suitable solvent to remove any dirt, grease, or contaminants.
-
Roughening: For smooth plastics, sanding or etching the surface increases its surface area and improves mechanical interlocking with the adhesive. Fiberglass often benefits from sanding to remove any loose fibers or resin.
-
Priming (if necessary): Certain plastics require a primer to improve adhesion. The primer acts as a bridge between the plastic's surface and the adhesive.
Step-by-Step Guide to Bonding Fiberglass to Plastic
- Select the appropriate adhesive. Consider the types of plastic and fiberglass and the application's stress level.
- Clean and prepare the surfaces. Thoroughly clean, and roughen surfaces as needed. Apply a primer if necessary.
- Apply the adhesive. Follow the manufacturer's instructions meticulously.
- Clamp or secure the parts. Ensure proper alignment and apply pressure as needed.
- Allow for curing. Allow ample time for the adhesive to cure completely, according to the manufacturer's instructions.
Conclusion: Achieving a Durable Bond
Bonding fiberglass to plastic is achievable with the right approach. Understanding the specific challenges presented by different plastic types, selecting the appropriate adhesive, and performing meticulous surface preparation are all crucial for achieving a strong and durable bond. Remember to always consult the manufacturer's instructions for your chosen adhesive and materials for optimal results. By carefully following these steps, you can successfully bond fiberglass to plastic for a wide range of applications.
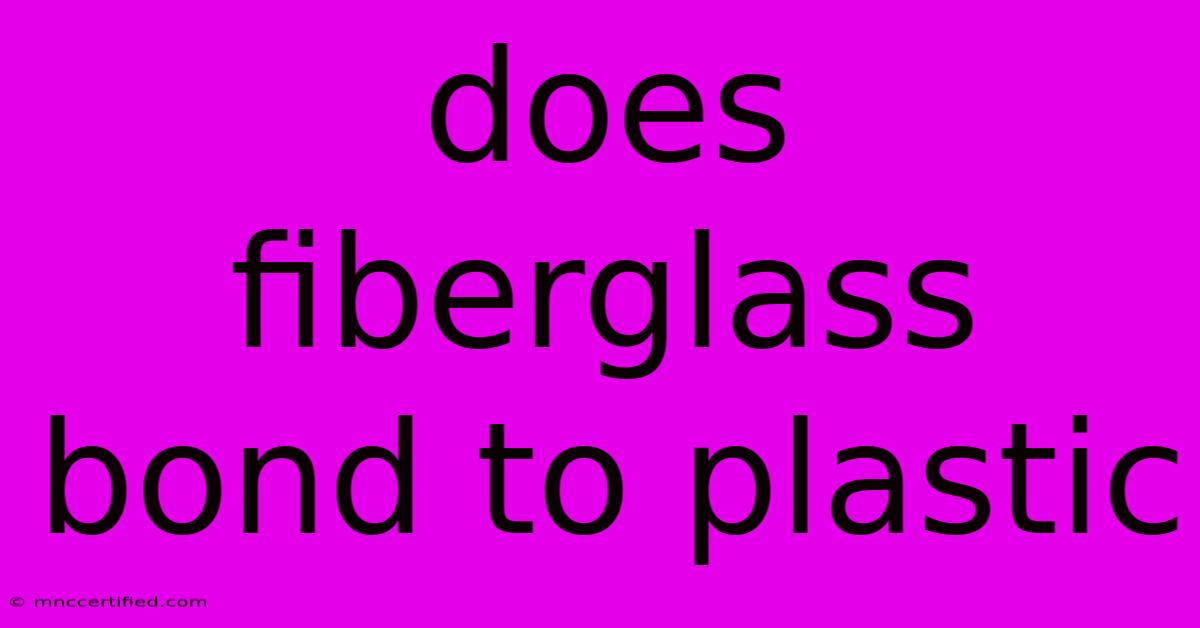
Thank you for visiting our website wich cover about Does Fiberglass Bond To Plastic. We hope the information provided has been useful to you. Feel free to contact us if you have any questions or need further assistance. See you next time and dont miss to bookmark.
Featured Posts
-
Icc Arrest Warrants Israel And Hamas Leaders
Nov 22, 2024
-
India Vs Australia Test Live Stream Details
Nov 22, 2024
-
Trading Card Stores In San Diego
Nov 22, 2024
-
Nfl Browns Defeat Steelers 24 19
Nov 22, 2024
-
Texas Bonded Title Out Of State
Nov 22, 2024