Fusion Bonded Epoxy Pipe Coating
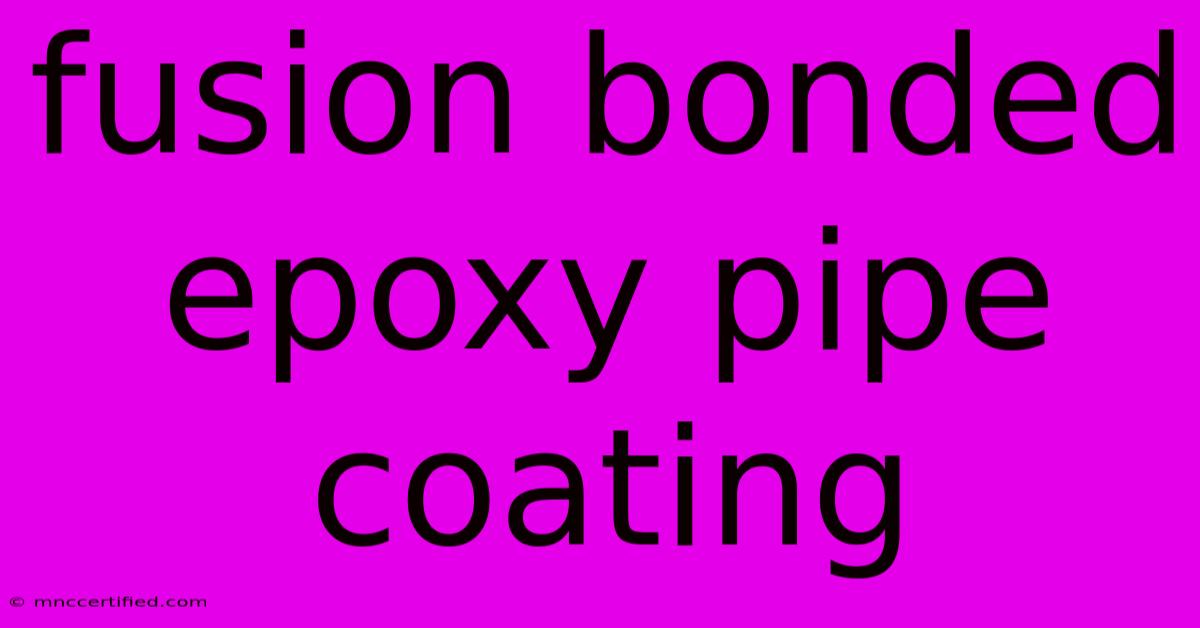
Table of Contents
Fusion Bonded Epoxy (FBE) Pipe Coating: A Comprehensive Guide
Fusion bonded epoxy (FBE) coating is a highly effective and widely used protective layer for steel pipes, particularly in the oil and gas, and water transmission industries. This comprehensive guide delves into the intricacies of FBE pipe coating, exploring its application, benefits, and limitations. Understanding FBE coating is crucial for anyone involved in pipeline construction, maintenance, or management.
What is Fusion Bonded Epoxy Coating?
Fusion bonded epoxy (FBE) coating is a thermosetting powder coating that chemically bonds with the surface of the steel pipe at a high temperature. This process creates a robust, impermeable barrier that protects against corrosion, abrasion, and other environmental factors. Unlike other coatings that simply adhere to the pipe's surface, FBE coating achieves a truly integral bond, resulting in superior performance and longevity. The process involves meticulously preparing the pipe surface, applying the epoxy powder, and then curing it in a precisely controlled oven.
Key Components of FBE Coating:
- Epoxy Resin: This forms the base of the coating, providing its chemical resistance, adhesion, and mechanical strength.
- Curing Agent: This initiates the chemical reaction that hardens the epoxy resin, transforming it from a powder into a solid, durable coating.
- Additives: These may include pigments for color, fillers to improve specific properties, and flow control agents to ensure smooth application.
Benefits of Fusion Bonded Epoxy Pipe Coating
FBE coating offers a multitude of advantages, making it the preferred choice for many pipeline projects:
- Exceptional Corrosion Resistance: FBE provides outstanding protection against corrosion caused by soil, water, and other aggressive environments. This significantly extends the lifespan of the pipeline and reduces maintenance costs.
- High Mechanical Strength: The cured epoxy coating boasts excellent impact resistance and abrasion resistance, protecting against damage from handling and transportation.
- Excellent Electrical Insulation: FBE acts as an effective electrical insulator, preventing stray currents that can lead to corrosion. This is especially crucial in underground pipelines.
- Ease of Application: While the curing process requires specialized equipment, the application of FBE powder coating is relatively efficient and consistent, leading to high-quality results.
- Cost-Effective: While the initial investment might seem higher compared to some other coatings, the extended lifespan and reduced maintenance requirements make FBE a cost-effective solution in the long run.
- Environmentally Friendly: FBE coatings are typically low in volatile organic compounds (VOCs), contributing to a more environmentally responsible approach to pipeline protection.
The FBE Coating Application Process
The application process involves several critical steps:
- Surface Preparation: This is arguably the most crucial step. The steel pipe must be meticulously cleaned to remove mill scale, rust, and other contaminants. This often involves abrasive blasting to achieve a suitable surface profile for optimal adhesion.
- Preheating: The pipe is preheated to ensure proper fusion with the epoxy powder.
- Powder Application: The epoxy powder is electrostatically sprayed onto the preheated pipe.
- Curing: The coated pipe is then passed through a precisely controlled oven where the epoxy powder fuses with the steel and cures to form a continuous, protective layer.
- Inspection and Testing: After curing, rigorous inspection and testing are conducted to ensure the coating meets specified standards. This often involves visual inspection, holiday detection (to identify pinholes or discontinuities), and thickness measurements.
Limitations of FBE Coating
While FBE coating offers numerous benefits, it's essential to acknowledge its limitations:
- Temperature Sensitivity: FBE coatings have a temperature operating range. Exposure to extremely high temperatures can degrade the coating's performance.
- UV Degradation: While resistant to many environmental factors, prolonged exposure to UV radiation can lead to some degree of degradation over time, particularly in above-ground applications.
- Damage Susceptibility: While strong, FBE is susceptible to damage from mechanical impact or abrasion. Proper handling and installation are crucial to avoid compromising the coating's integrity.
Conclusion: Choosing the Right Pipe Coating
Fusion bonded epoxy coating offers a compelling solution for protecting steel pipelines in various demanding environments. Its exceptional corrosion resistance, mechanical strength, and cost-effectiveness make it a preferred choice for many projects. However, careful consideration of the specific application conditions, potential limitations, and proper installation techniques is crucial for maximizing its effectiveness and achieving long-term success. For optimal results, consulting with experienced professionals in pipeline coating is highly recommended.
Keywords: Fusion bonded epoxy coating, FBE coating, pipe coating, pipeline protection, corrosion protection, epoxy coating, steel pipe coating, oil and gas pipelines, water pipelines, pipeline maintenance, coating application, coating inspection.
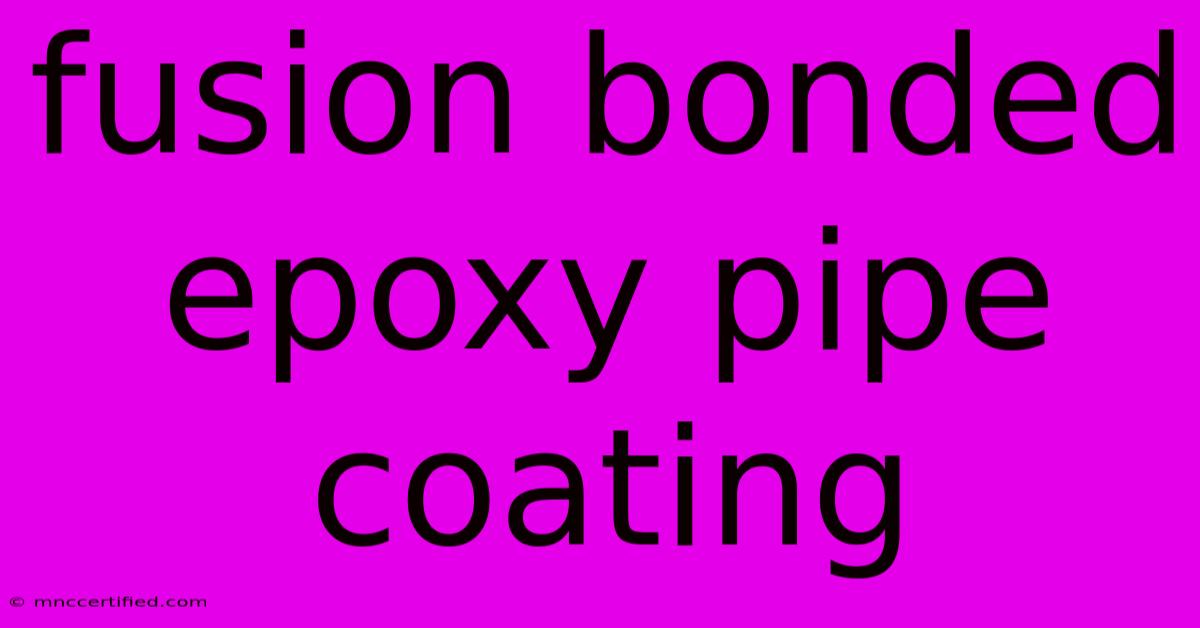
Thank you for visiting our website wich cover about Fusion Bonded Epoxy Pipe Coating. We hope the information provided has been useful to you. Feel free to contact us if you have any questions or need further assistance. See you next time and dont miss to bookmark.
Featured Posts
-
Tesco Salmonella Recall Check Your Product
Nov 20, 2024
-
Marvel Comics Trading Cards Value
Nov 20, 2024
-
Investment Properties In Maryland
Nov 20, 2024
-
Jaguars New Logo Ja G Uar
Nov 20, 2024
-
25 Cold Weather Payments Eligible Postcodes
Nov 20, 2024