Glue To Bond Plastic To Metal
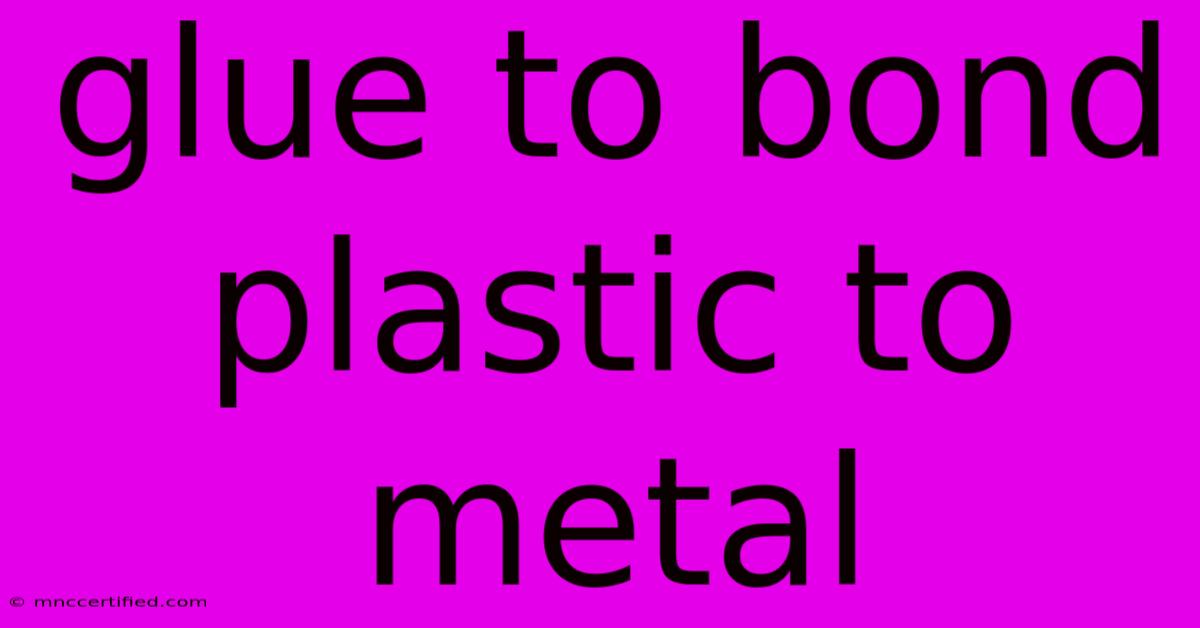
Table of Contents
The Ultimate Guide to Bonding Plastic to Metal: Choosing the Right Adhesive
Choosing the right glue to bond plastic to metal can be tricky. The success of your project hinges on selecting an adhesive compatible with both materials and capable of withstanding the intended stress and environmental conditions. This comprehensive guide will explore various adhesive types, application techniques, and crucial factors to consider for a strong and lasting bond.
Understanding the Challenges of Bonding Plastic to Metal
Plastic and metal possess vastly different surface properties. Metals are typically more rigid and have higher surface energy, while plastics are often more flexible and have lower surface energy. This difference in surface characteristics makes achieving a strong, reliable bond challenging. Poor adhesion often results from insufficient surface preparation or the selection of an incompatible adhesive.
Key Challenges:
- Surface Energy Differences: Plastics often require specialized surface treatments to improve adhesion.
- Coefficient of Thermal Expansion: Differing expansion rates between plastic and metal can lead to bond failure under fluctuating temperatures.
- Chemical Compatibility: The chemical composition of both the plastic and metal needs to be considered when choosing an adhesive. Certain plastics and metals can react negatively with certain adhesives.
Types of Adhesives for Bonding Plastic to Metal
Several adhesive types excel at bonding plastic to metal, each with its own strengths and weaknesses.
1. Epoxy Adhesives: The Workhorse
Epoxy adhesives are a popular choice due to their versatility, high strength, and excellent resistance to various environmental factors, including chemicals and temperature fluctuations. Two-part epoxy systems require mixing the resin and hardener before application, providing a longer working time and allowing for precise placement. Key advantages include high shear strength and excellent gap-filling capabilities. However, cure times can be relatively long.
2. Cyanoacrylate (Super Glue): Fast and Convenient
Cyanoacrylate adhesives, commonly known as super glue, offer incredibly fast bonding times. They are easy to use and ideal for small, precise applications. However, their strength and durability can be less than epoxy adhesives, and they may not be suitable for all plastic types. Consider this option for smaller projects needing a quick fix.
3. Urethane Adhesives: Flexibility and Durability
Urethane adhesives provide a good balance of strength, flexibility, and durability. They are suitable for applications where some flexibility is needed to accommodate the different thermal expansion rates of plastic and metal. Their toughness makes them a good choice for applications subject to vibration or impact.
4. Acrylic Adhesives: Versatile and User-Friendly
Acrylic adhesives are versatile and user-friendly, offering good adhesion to various plastics and metals. They are typically solvent-based or water-based, providing different curing mechanisms. Water-based options are often preferred for their lower VOC (volatile organic compound) emissions.
Preparing Surfaces for Optimal Bonding
Proper surface preparation is paramount for a successful bond. This involves:
- Cleaning: Remove all dirt, grease, oil, and other contaminants from both surfaces using a suitable solvent like isopropyl alcohol.
- Roughening: For many plastics, increasing surface roughness through mechanical abrasion (sanding) or chemical etching improves adhesion. This provides more surface area for the adhesive to grip.
- Priming: In some cases, a primer may be necessary to improve adhesion between the adhesive and the substrate. Primers are specifically designed to improve the wettability of the surface and enhance the bond strength.
Choosing the Right Adhesive: Factors to Consider
Before selecting an adhesive, carefully consider these factors:
- Type of Plastic: Different plastics (ABS, polycarbonate, polypropylene, etc.) have varying levels of compatibility with different adhesives. Check the adhesive manufacturer's specifications for compatibility.
- Type of Metal: The type of metal (steel, aluminum, etc.) can also influence adhesive selection.
- Environmental Conditions: Consider the temperature range, humidity, and chemical exposure the bond will be subjected to.
- Strength Requirements: Determine the required strength based on the application's intended use and stress levels.
- Cure Time: Select an adhesive with a cure time that fits your project timeline.
Application Techniques for Success
Follow the adhesive manufacturer's instructions carefully. Generally, a thin, even layer of adhesive is applied to both surfaces, pressed together, and clamped or weighted to ensure proper contact during curing.
Conclusion: Strong Bonds Start with Careful Selection
Bonding plastic to metal successfully requires meticulous planning and execution. By understanding the challenges, selecting the appropriate adhesive, preparing surfaces effectively, and following proper application techniques, you can achieve strong, durable, and long-lasting bonds for your projects. Remember to always consult the manufacturer's instructions for specific application details and safety precautions.
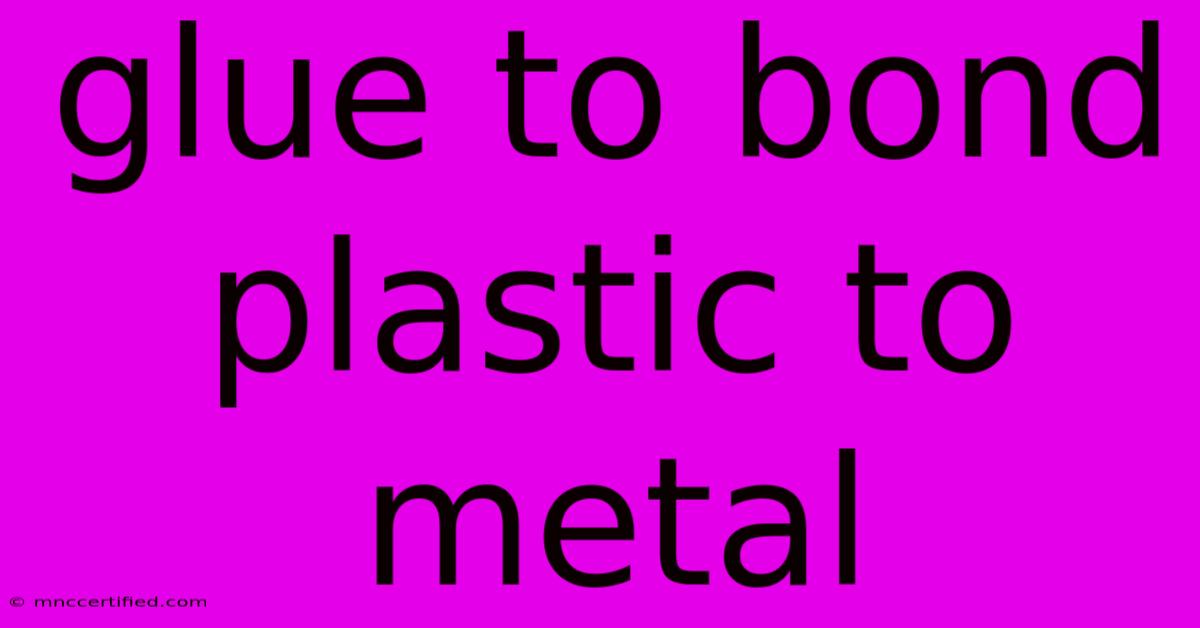
Thank you for visiting our website wich cover about Glue To Bond Plastic To Metal. We hope the information provided has been useful to you. Feel free to contact us if you have any questions or need further assistance. See you next time and dont miss to bookmark.
Featured Posts
-
Liverpools Tsimikas Suffers Injury
Nov 28, 2024
-
Live Liverpool Real Madrid Ucl Recap
Nov 28, 2024
-
Trading A Motorcycle For A Car
Nov 28, 2024
-
Johnny Sins And Savannah Bond
Nov 28, 2024
-
Euromillions Results Update Check Tickets
Nov 28, 2024