How To Bond Aluminum To Aluminum
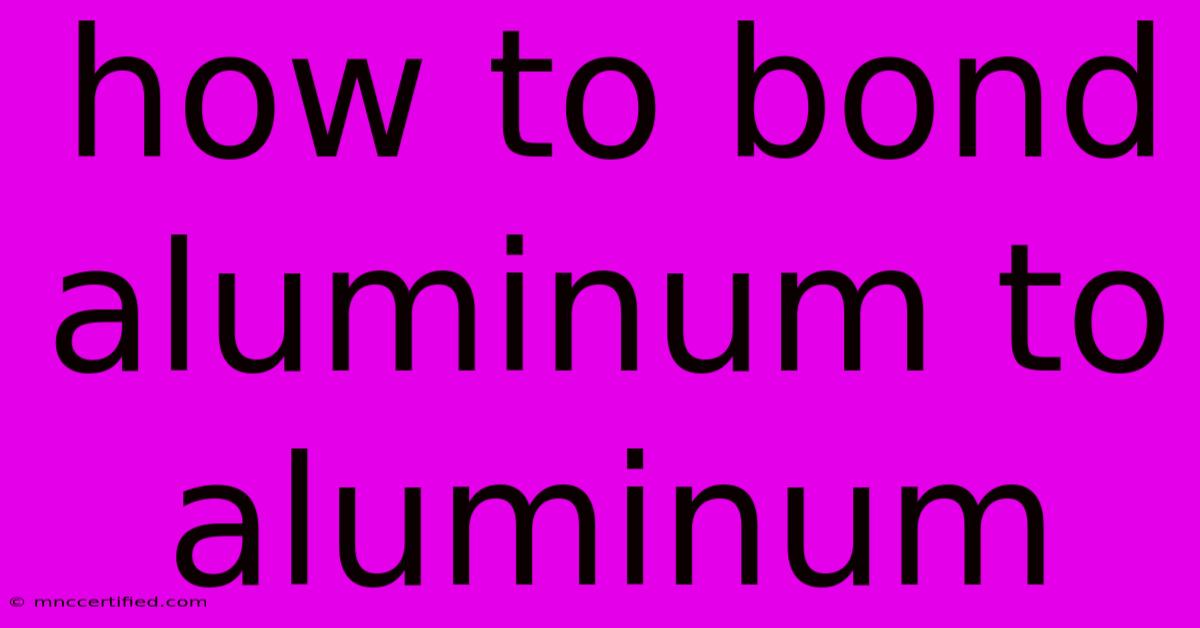
Table of Contents
How to Bond Aluminum to Aluminum: A Comprehensive Guide
Aluminum's lightweight yet strong nature makes it a popular choice in various industries, from aerospace to automotive. Often, joining aluminum components requires a strong, reliable bond. This comprehensive guide explores various methods for bonding aluminum to aluminum, covering their strengths, weaknesses, and best applications. We'll delve into the crucial preparation steps, ensuring you achieve a lasting, high-quality bond.
Understanding Aluminum Bonding Challenges
Before exploring bonding methods, it's crucial to understand the inherent challenges of working with aluminum. Its surface readily forms a thin, tenacious oxide layer (aluminum oxide) which hinders adhesion. This oxide layer is passive, meaning it protects the underlying aluminum from further oxidation but also acts as a barrier, preventing proper bonding. Therefore, thorough surface preparation is paramount for successful aluminum-to-aluminum bonding.
Effective Methods for Bonding Aluminum to Aluminum
Several effective methods exist for creating strong, durable bonds between aluminum pieces. Each has its own advantages and disadvantages, making the choice dependent on the specific application and required bond strength.
1. Adhesive Bonding
Adhesive bonding offers a versatile and cost-effective solution for many aluminum-to-aluminum joining applications. Choosing the right adhesive is critical. Here are some key considerations:
-
Epoxy Adhesives: Epoxy adhesives are widely used for their high strength, versatility, and good resistance to environmental factors. Many formulations are available, offering varying degrees of flexibility and cure times. Look for epoxies specifically designed for aluminum bonding.
-
Cyanoacrylate (Super Glue): Cyanoacrylate adhesives offer fast curing times and excellent gap-filling capabilities. However, they are generally less strong than epoxies and less resistant to high temperatures or harsh chemicals.
-
Structural Adhesives: Designed for high-strength applications, these adhesives often require specialized surface preparation and curing conditions. They offer superior performance compared to standard epoxies for high-stress applications.
Preparation is key: Before applying any adhesive, meticulously clean the aluminum surfaces. This often involves degreasing with a solvent like acetone or isopropyl alcohol, followed by abrasive cleaning (e.g., with Scotchbrite pads) to remove the oxide layer and create a microscopically rough surface for improved adhesion. Precisely following the adhesive manufacturer's instructions regarding surface preparation, mixing ratios, and curing times is essential.
2. Welding
Welding offers the strongest bond for aluminum. However, it requires specialized equipment and expertise. Several welding techniques are suitable for aluminum:
-
Gas Tungsten Arc Welding (GTAW) or TIG Welding: This precision method produces high-quality welds but necessitates skill and practice.
-
Gas Metal Arc Welding (GMAW) or MIG Welding: Faster than TIG welding, MIG welding is suitable for thicker aluminum pieces.
-
Resistance Spot Welding: Ideal for joining sheet metal, this method uses electrical resistance to create a weld at the contact points.
Note: Proper shielding gas and filler materials are critical for successful aluminum welding. Improper technique can result in porosity, weakening the weld.
3. Mechanical Fasteners (Rivets, Bolts, Screws)
Mechanical fasteners are a straightforward method, particularly suitable for applications where disassembly might be necessary. However, they create holes in the aluminum components, potentially compromising structural integrity in some designs. Using appropriate fasteners and ensuring proper hole sizing are crucial.
4. Brazing
Brazing uses a filler metal with a lower melting point than the base metal to join the aluminum pieces. This requires specialized equipment and expertise to control the temperature precisely.
Optimizing Your Aluminum-to-Aluminum Bond
Regardless of the chosen method, these steps enhance bond strength and longevity:
-
Thorough Surface Preparation: This is arguably the most critical step. Remove all dirt, grease, oil, and the oxide layer.
-
Proper Adhesive Selection: Choose an adhesive specifically designed for aluminum and high-strength bonding.
-
Controlled Environment: Avoid extreme temperatures and humidity during the bonding process.
-
Correct Curing Time: Allow the adhesive sufficient time to cure according to the manufacturer's instructions.
-
Post-Bonding Inspection: Inspect the bond for any imperfections or weaknesses.
Conclusion: Choosing the Right Method
The best method for bonding aluminum to aluminum depends heavily on factors like the application, required strength, budget, and available equipment. Weigh the pros and cons of each method, carefully consider surface preparation, and follow manufacturer instructions precisely to achieve a durable and reliable bond. Remember, consulting with a materials specialist can be beneficial for complex applications.
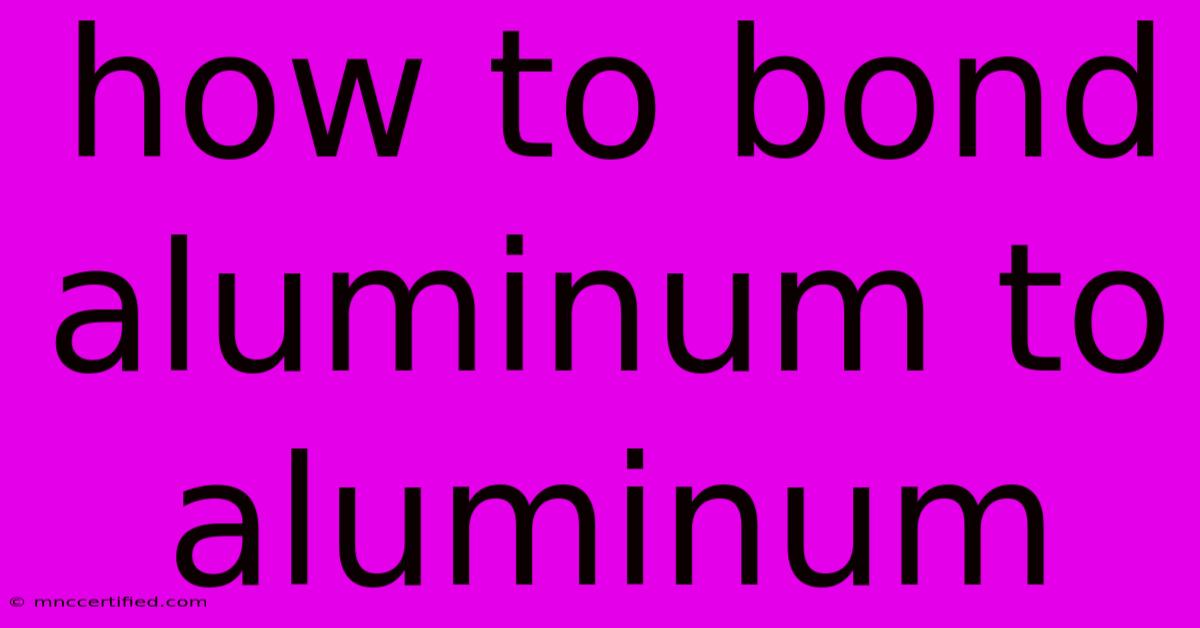
Thank you for visiting our website wich cover about How To Bond Aluminum To Aluminum. We hope the information provided has been useful to you. Feel free to contact us if you have any questions or need further assistance. See you next time and dont miss to bookmark.
Featured Posts
-
26 Foot Box Truck Insurance Cost
Nov 21, 2024
-
Megan Moroney Country Music Star
Nov 21, 2024
-
Shaboozey Sings Highway And A Bar Song
Nov 21, 2024
-
Songbird Crypto Price Prediction
Nov 21, 2024
-
War And Treaty 2024 Cma Nominees
Nov 21, 2024