How To Bond Metal To Plastic
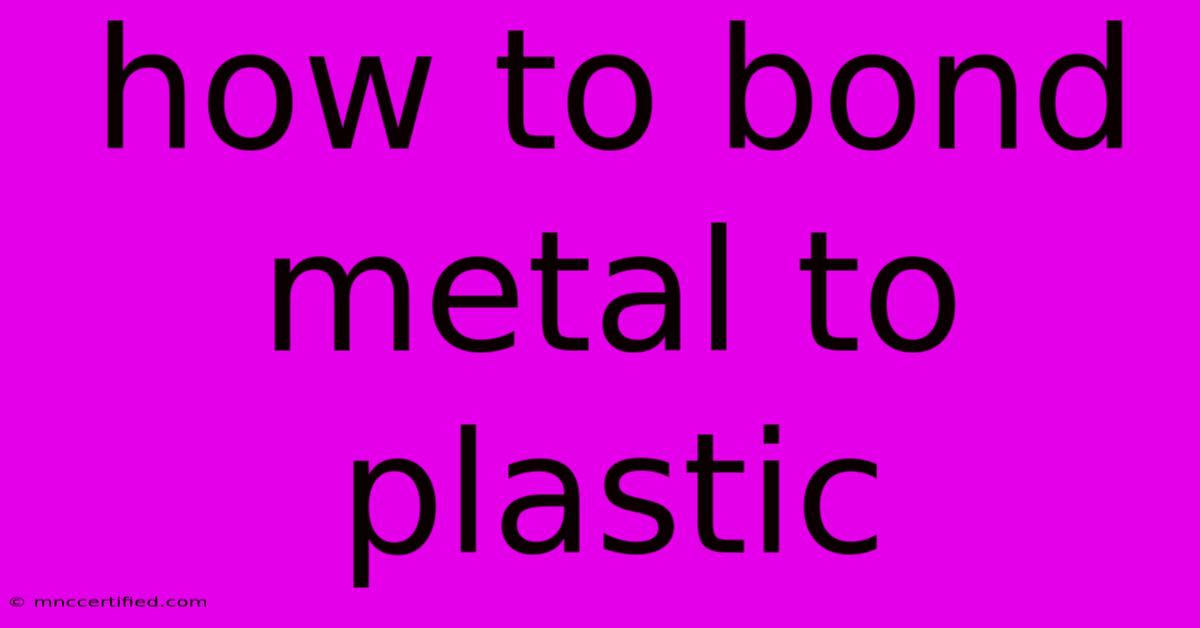
Table of Contents
How to Bond Metal to Plastic: A Comprehensive Guide
Bonding metal to plastic presents unique challenges due to the inherent differences in their material properties. Metals are typically rigid and conductive, while plastics are often flexible and insulating. Successfully joining these disparate materials requires careful consideration of surface preparation, adhesive selection, and proper application techniques. This comprehensive guide will walk you through the process, helping you achieve a strong and durable bond.
Understanding the Challenges: Why Metal-to-Plastic Bonding is Difficult
The difficulty in bonding metal to plastic stems from several factors:
- Surface Energy Differences: Metals generally have higher surface energy than plastics, meaning they are less receptive to adhesive bonding. Plastics can also have low surface energy, leading to poor wettability by the adhesive.
- Coefficient of Thermal Expansion: Metals and plastics have different coefficients of thermal expansion (CTE). This means they expand and contract at different rates with temperature changes, potentially leading to stress and bond failure.
- Material Compatibility: The choice of adhesive is crucial. Some adhesives may not adhere well to certain metal or plastic types. For example, certain plastics are chemically incompatible with specific adhesives.
Choosing the Right Adhesive: Key Factors to Consider
Selecting the appropriate adhesive is paramount for a successful bond. Key factors to consider include:
- Adhesive Type: Several adhesive types are suitable for metal-to-plastic bonding, including:
- Epoxy adhesives: Known for their strong bond strength, versatility, and resistance to various environmental factors. They are a popular choice for many metal-to-plastic applications.
- Cyanoacrylate (Super Glue): Offers fast curing times but may have lower strength and durability compared to epoxies, particularly under stress or extreme temperatures. Best suited for smaller, less demanding applications.
- Polyurethane adhesives: Provide good flexibility and impact resistance, making them suitable for applications where the bond needs to withstand vibrations or flexing.
- Acrylic adhesives: Offer good adhesion to a variety of substrates, including some plastics and metals. They are often chosen for their ease of application.
- Plastic Type: The type of plastic (e.g., ABS, polycarbonate, polypropylene) significantly impacts adhesive selection. Some plastics require specific primers or surface treatments to ensure proper adhesion.
- Metal Type: The metal's surface finish and type also influence adhesive choice. Certain metals might react with specific adhesives.
- Application Requirements: Consider the intended use of the bonded assembly. Will it be exposed to high temperatures, chemicals, or significant stress? The adhesive must withstand these conditions.
Primer Selection: Often Essential for Success
Primers enhance the adhesion of the adhesive to both the metal and the plastic surfaces. They improve surface wettability and provide a better mechanical interlock, leading to a stronger bond. Always check the adhesive manufacturer's recommendations for primer compatibility.
Surface Preparation: The Foundation of a Strong Bond
Proper surface preparation is critical for optimal adhesion. This typically involves:
- Cleaning: Thoroughly clean both the metal and plastic surfaces to remove any dirt, grease, oil, or other contaminants. Use appropriate solvents like isopropyl alcohol or specialized cleaning agents recommended by the adhesive manufacturer.
- Abrasion: Lightly abrade the surfaces using sandpaper or a suitable abrasive media. This creates a rougher surface, increasing the surface area for better adhesive bonding. Avoid excessive abrasion, which could damage the substrate.
- Degreasing: After cleaning and abrasion, degrease the surfaces again to ensure complete removal of any residue.
Bonding Techniques: A Step-by-Step Guide
The specific application method will vary depending on the adhesive type. However, these general steps apply:
- Apply Primer (if necessary): Follow the manufacturer's instructions for primer application. Allow sufficient drying time before proceeding.
- Apply Adhesive: Dispense the adhesive according to the manufacturer's guidelines. Even application is essential for a uniform bond line.
- Join the Surfaces: Quickly and firmly press the metal and plastic surfaces together. Ensure proper alignment and apply even pressure to distribute the adhesive.
- Curing: Allow the adhesive to cure completely. The curing time varies depending on the adhesive type and environmental conditions. Refer to the manufacturer's specifications.
- Post-Cure (if necessary): Some adhesives benefit from post-curing at elevated temperatures to enhance bond strength.
Troubleshooting Common Bonding Problems
- Weak Bond: Insufficient surface preparation, incorrect adhesive selection, or improper curing are common causes of weak bonds.
- Bond Failure: Temperature changes, chemical exposure, or excessive stress can lead to bond failure. Ensure the adhesive is compatible with the intended environment and application.
- Uneven Bonding: Uneven adhesive application or insufficient pressure during bonding can result in an uneven bond.
By following these steps and carefully considering the factors discussed, you can successfully bond metal to plastic, achieving a durable and reliable connection. Remember to always consult the adhesive manufacturer's instructions for specific recommendations and safety precautions. This will help ensure the best possible results for your project.
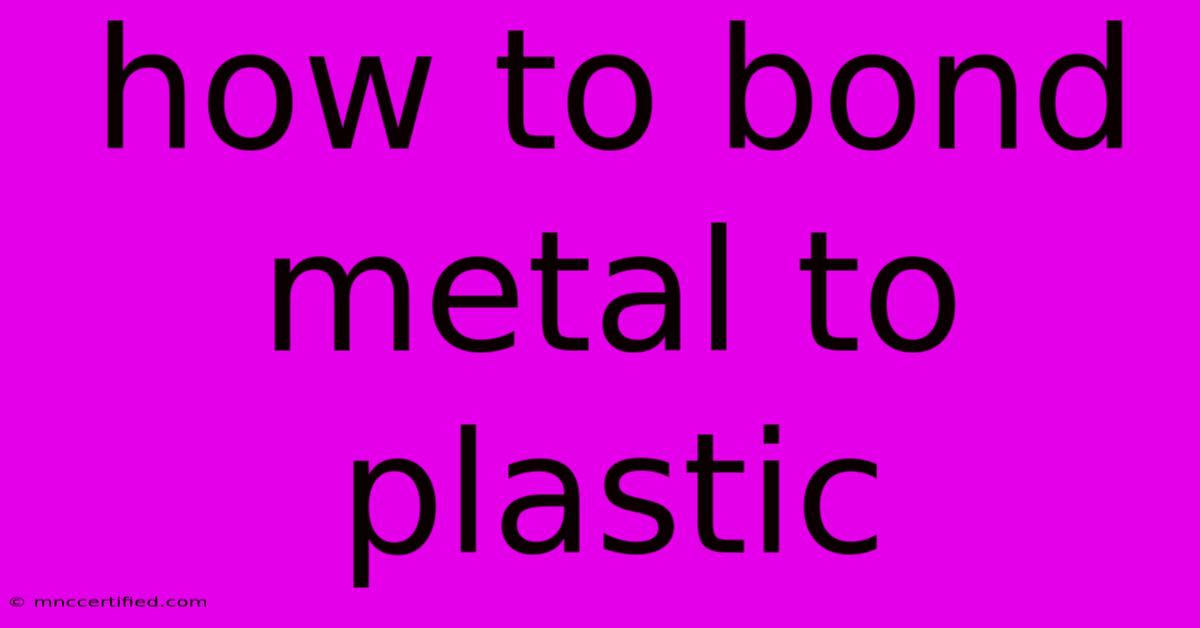
Thank you for visiting our website wich cover about How To Bond Metal To Plastic. We hope the information provided has been useful to you. Feel free to contact us if you have any questions or need further assistance. See you next time and dont miss to bookmark.
Featured Posts
-
Bond Arms Cross Draw Holster
Nov 30, 2024
-
Who Is The Obligee On A Bond
Nov 30, 2024
-
Wisconsin Vs Minnesota Game Live Stream Info
Nov 30, 2024
-
Thanksgiving Affleck Garner Together
Nov 30, 2024
-
Does Bondo Stick To Aluminum
Nov 30, 2024