How To Bond Plastic To Metal
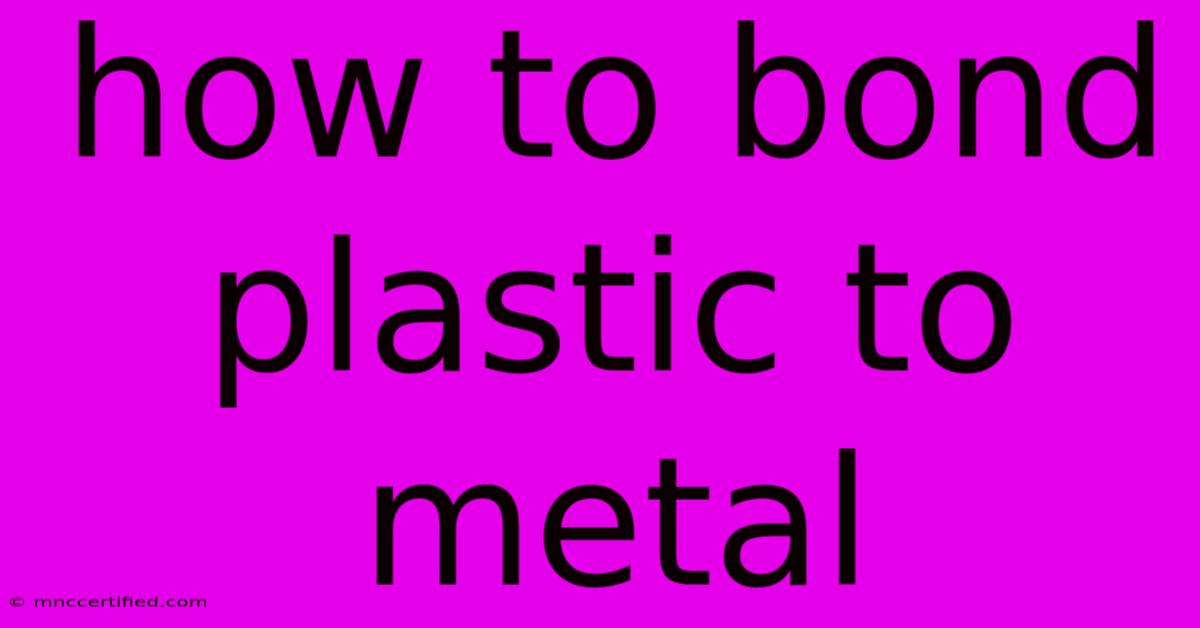
Table of Contents
How to Bond Plastic to Metal: A Comprehensive Guide
Bonding plastic to metal presents unique challenges due to the different surface properties of these materials. Unlike bonding similar materials, achieving a strong, lasting bond requires careful surface preparation and the selection of the right adhesive. This comprehensive guide will walk you through the process, helping you achieve a successful bond every time.
Understanding the Challenges: Plastic vs. Metal
The key challenge lies in the inherent differences between plastics and metals. Metals are generally denser and more rigid, often possessing a smooth, non-porous surface. Plastics, on the other hand, can be more porous, flexible, and have varying surface energies. This difference in surface properties affects the adhesion of the adhesive. A successful bond requires maximizing the contact area between the adhesive, plastic, and metal.
Factors Affecting Bond Strength:
- Surface Energy: A higher surface energy promotes better wetting and adhesion. Plastics often have lower surface energy than metals, requiring surface treatment to enhance bonding.
- Surface Roughness: A rougher surface provides more mechanical interlocking for the adhesive, increasing bond strength.
- Chemical Compatibility: The adhesive must be chemically compatible with both the plastic and the metal to ensure a strong bond. Choosing the wrong adhesive can lead to failure.
- Temperature and Pressure: Applying heat and pressure during the curing process can significantly improve bond strength.
Step-by-Step Guide to Bonding Plastic to Metal
This process requires precision and attention to detail. Here's a detailed step-by-step guide:
1. Surface Preparation: The Foundation of a Strong Bond
This is arguably the most crucial step. Improper surface preparation will lead to adhesive failure.
- Cleaning: Thoroughly clean both the plastic and metal surfaces using a suitable solvent to remove grease, oil, dirt, and any other contaminants. Isopropyl alcohol (IPA) is a common choice.
- Abrasion: Increase surface roughness through abrasion. For plastics, you might use fine-grit sandpaper (e.g., 200-400 grit) or a chemical etching process depending on the plastic type. For metals, sanding or wire brushing can be effective. The goal is to create a microscopically rough surface for better mechanical interlocking.
- Priming (Often Necessary): Applying a primer specifically designed for the plastic and metal types enhances adhesion. Primers improve surface energy and promote better wetting by the adhesive. Always consult the adhesive manufacturer's instructions for recommended primers.
2. Adhesive Selection: Choosing the Right Partner
The type of adhesive you choose will depend on several factors, including:
- The types of plastic and metal: Different plastics and metals require different adhesives. Consult adhesive datasheets to ensure compatibility.
- The application's environmental conditions: Consider temperature extremes, exposure to chemicals, and other environmental factors that could affect bond strength.
- The desired bond strength: High-strength applications might require structural adhesives, while less demanding applications might use lower-strength options. Options include epoxy resins, cyanoacrylates (super glue), polyurethane adhesives, and specialized plastic-to-metal adhesives.
3. Adhesive Application: Precision and Technique
- Even Application: Apply the adhesive evenly to both surfaces, ensuring complete coverage. Follow the manufacturer's instructions regarding application thickness.
- Fixturing: Use clamps or other fixturing methods to hold the parts together during curing, ensuring consistent pressure and alignment.
- Curing: Allow the adhesive to cure completely according to the manufacturer's instructions. This may involve specific temperature and pressure settings.
4. Post-Bonding Inspection: Ensuring Success
After the adhesive has cured, inspect the bond for any imperfections. Look for signs of adhesive failure, such as gaps or weak points. A properly bonded joint should be strong and stable.
Tips for Success:
- Always consult the adhesive manufacturer's instructions: This is paramount for successful bonding.
- Proper ventilation: Many adhesives release fumes, so work in a well-ventilated area.
- Safety precautions: Wear appropriate personal protective equipment (PPE), such as gloves and eye protection.
- Test your bond: Before committing to a large-scale project, perform small-scale tests to ensure the bond strength meets your requirements.
By following these steps and carefully considering the factors outlined above, you can successfully bond plastic to metal and create durable, long-lasting joints. Remember that preparation is key, and choosing the right adhesive is crucial for achieving optimal results.
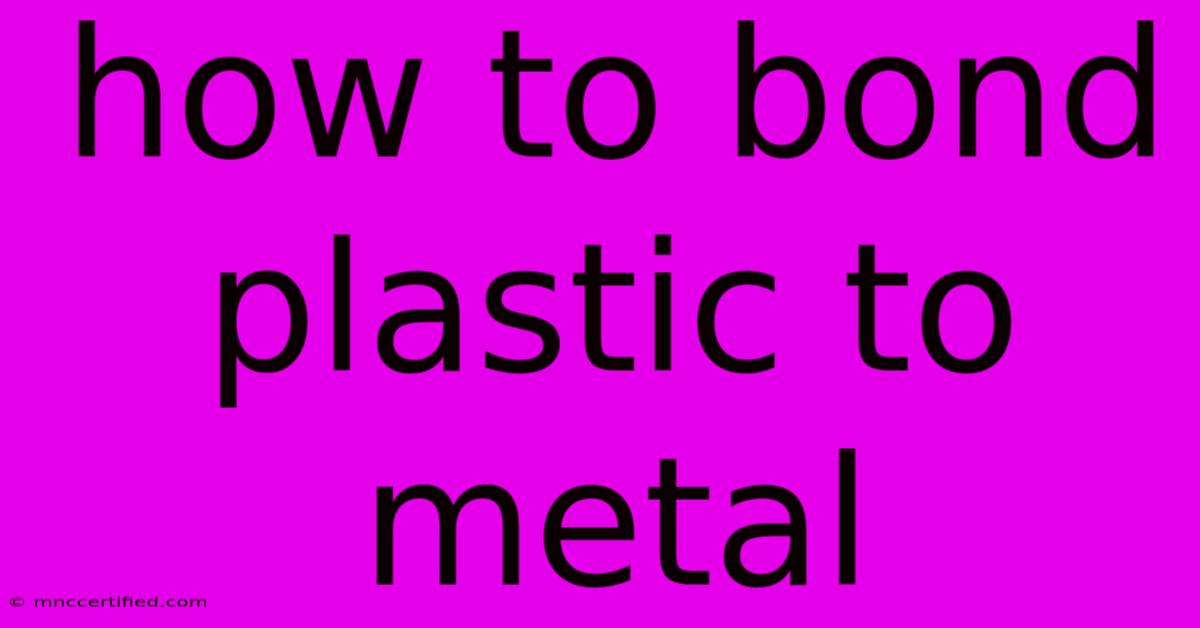
Thank you for visiting our website wich cover about How To Bond Plastic To Metal. We hope the information provided has been useful to you. Feel free to contact us if you have any questions or need further assistance. See you next time and dont miss to bookmark.
Featured Posts
-
Las Vegas Aladdin Bail Bonds
Nov 30, 2024
-
Sephora Black Friday Sale Up To 50 Off
Nov 30, 2024
-
Aladdin Bail Bonds Inglewood
Nov 30, 2024
-
Air Pods Black Friday 2024 Deals
Nov 30, 2024
-
Rivalry Week College Football Scenarios
Nov 30, 2024