Investment Cast Stainless Steel
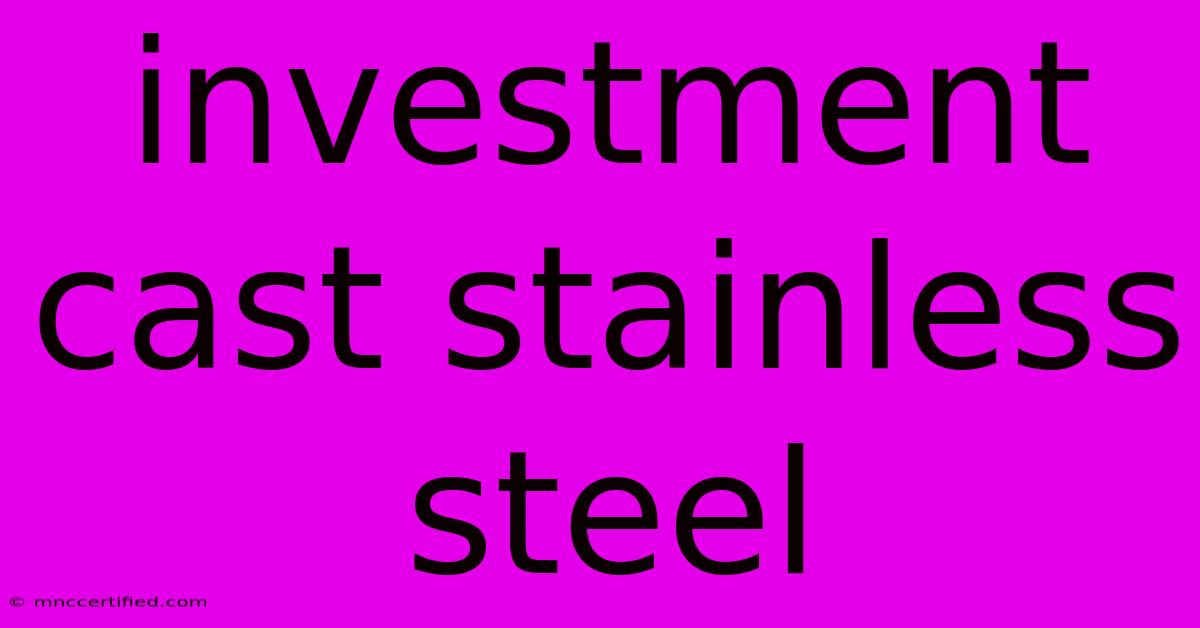
Table of Contents
Investment Cast Stainless Steel: A Superior Choice for Demanding Applications
Investment casting, also known as lost-wax casting, is a highly precise manufacturing process ideal for creating intricate and complex parts. When combined with the exceptional properties of stainless steel, it yields components with superior strength, corrosion resistance, and durability. This article delves into the specifics of investment cast stainless steel, exploring its advantages, applications, and the factors influencing its cost.
What is Investment Cast Stainless Steel?
Investment cast stainless steel involves creating a wax pattern of the desired part, which is then coated in a ceramic shell. The wax is melted out, leaving a cavity into which molten stainless steel is poured. After cooling and solidifying, the ceramic shell is removed, revealing the finished stainless steel component. This method allows for the production of highly detailed parts with complex geometries, thin walls, and tight tolerances – something often impossible with other casting methods. The process is particularly well-suited for high-value, low-volume production runs.
Advantages of Investment Cast Stainless Steel
Investment casting offers several key advantages when using stainless steel as the base material:
-
Exceptional Detail and Complexity: The process excels at producing parts with intricate designs and features that are difficult or impossible to achieve with other manufacturing techniques like machining or forging. This is crucial for applications requiring detailed components.
-
Superior Dimensional Accuracy and Surface Finish: Investment casting produces parts with very tight tolerances and a smooth surface finish, minimizing the need for secondary machining operations. This reduces manufacturing time and cost.
-
Excellent Material Properties: Stainless steel's inherent properties – high strength, corrosion resistance, and durability – are perfectly complemented by the precision of investment casting. This combination results in high-performance parts capable of withstanding demanding environments.
-
Wide Range of Stainless Steel Grades: The process can accommodate various stainless steel grades, allowing for customization based on specific application requirements. From austenitic 304 and 316 to martensitic 410 and duplex grades, the choice is extensive.
-
Near-Net Shape Capability: Minimizes material waste, offering cost-effectiveness, particularly for intricate designs where significant material removal would be needed with other processes.
Applications of Investment Cast Stainless Steel
The unique properties of investment cast stainless steel make it ideal for a wide array of applications across numerous industries:
-
Aerospace: Turbine blades, engine components, and other critical parts where high strength, corrosion resistance, and precision are paramount.
-
Medical: Implants, surgical instruments, and other medical devices requiring biocompatibility and high hygiene standards.
-
Automotive: Engine components, exhaust manifolds, and other parts exposed to high temperatures and corrosive environments.
-
Oil and Gas: Valves, fittings, and other components used in harsh offshore and onshore applications.
-
Marine: Propulsion components, pumps, and other parts subjected to saltwater corrosion.
Factors Influencing the Cost of Investment Cast Stainless Steel
Several factors contribute to the overall cost of investment cast stainless steel components:
-
Complexity of the Design: Intricate designs require more time and materials, increasing the cost.
-
Stainless Steel Grade: Higher-grade stainless steels with enhanced properties often command a higher price.
-
Production Volume: Larger production runs generally lead to economies of scale, resulting in lower per-unit costs.
-
Surface Finish Requirements: Achieving a very fine surface finish may require additional processing, affecting the final cost.
Choosing the Right Investment Caster
Selecting a reputable investment casting provider is crucial to ensure high-quality parts. Look for casters with experience in stainless steel casting, a proven track record, and capabilities to meet your specific design and production requirements. Thorough due diligence is essential before committing to a supplier.
Conclusion
Investment cast stainless steel offers a compelling combination of precision, material properties, and versatility. Understanding its advantages, applications, and cost factors empowers engineers and designers to make informed decisions for projects demanding high-performance, durable, and corrosion-resistant components. By carefully considering the design, material selection, and production volume, businesses can leverage the benefits of this superior manufacturing process.
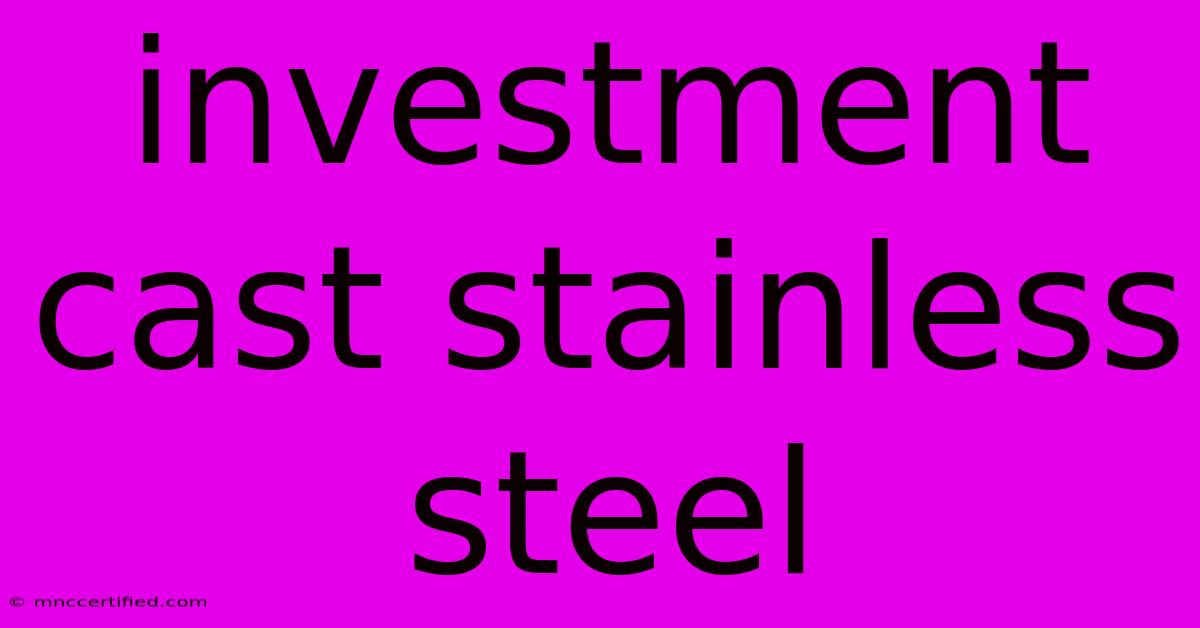
Thank you for visiting our website wich cover about Investment Cast Stainless Steel. We hope the information provided has been useful to you. Feel free to contact us if you have any questions or need further assistance. See you next time and dont miss to bookmark.
Featured Posts
-
State Farm Beekeeping Insurance
Nov 26, 2024
-
Valley Events This Week Top Picks
Nov 26, 2024
-
Db Cooper Mystery Solved After 53 Years
Nov 26, 2024
-
Omaha Beach Investment Holdings
Nov 26, 2024
-
Nile Cruise Egypts Ancient Wonders
Nov 26, 2024