Investment Casting Surface Finish
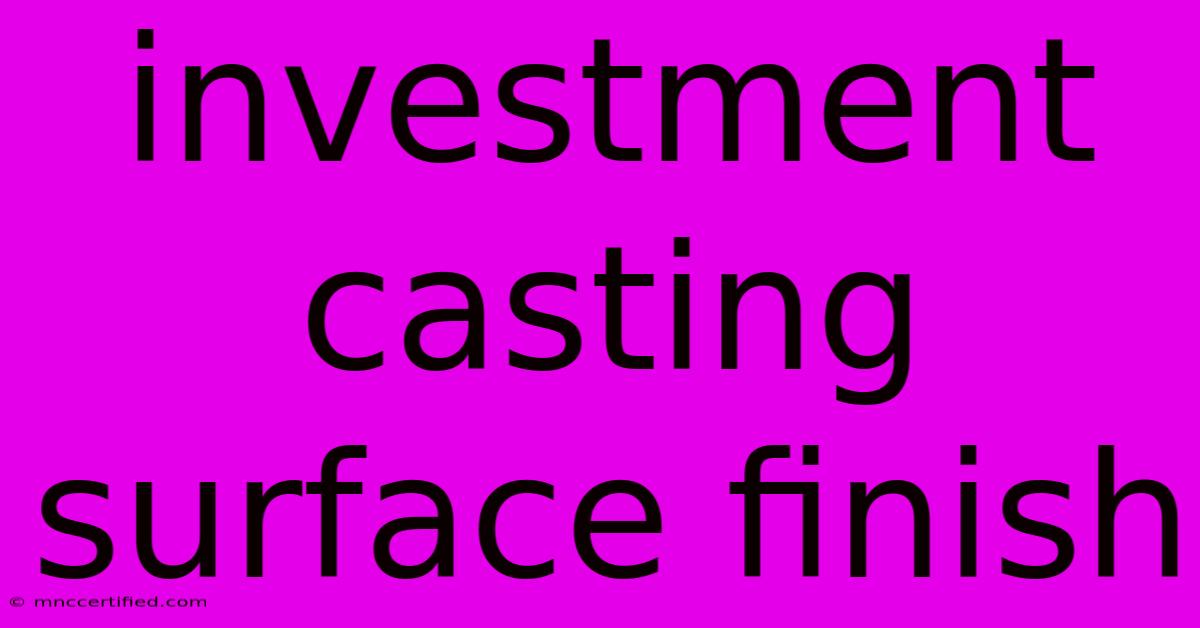
Table of Contents
Investment Casting Surface Finish: A Comprehensive Guide
Investment casting, also known as lost-wax casting, offers exceptional detail and intricate designs. However, the surface finish of investment castings isn't always perfect straight out of the mold. Understanding the factors influencing surface finish and available improvement methods is crucial for achieving the desired aesthetic and functional properties. This comprehensive guide explores investment casting surface finish in detail, helping you navigate the process and achieve optimal results.
Factors Affecting Investment Casting Surface Finish
Several factors contribute to the final surface finish of an investment casting. Understanding these factors is the first step to controlling and improving the quality:
1. Wax Pattern Quality: The Foundation of a Fine Finish
The quality of the wax pattern directly impacts the final casting. Imperfections in the wax, such as surface scratches, seams, or air bubbles, will be replicated in the casting. Therefore, investing in high-quality wax patterns and meticulous pattern-making techniques is paramount.
2. Mold Material and Preparation: Crucial for Consistency
The investment material used to create the mold significantly affects the surface finish. The choice of material, its consistency, and proper mixing are critical. Improper mixing or the presence of air bubbles in the mold can lead to surface imperfections. Careful mold preparation, including proper venting and preheating, is equally important.
3. Casting Process Parameters: Optimizing for Quality
Several parameters during the casting process itself affect the final surface finish. These include:
- Melting temperature: Maintaining the correct metal melting temperature is vital to prevent defects like porosity.
- Pouring temperature: The temperature of the molten metal at the time of pouring impacts the final surface.
- Pouring technique: A smooth, controlled pouring process helps prevent turbulence and surface defects.
- Cooling rate: A properly controlled cooling rate minimizes stresses and potential surface cracking.
4. Metal Properties: Inherent Characteristics
The metal being cast also plays a role. Some metals are inherently prone to surface imperfections, requiring more refined processing techniques. Understanding the specific properties of the metal being used is crucial for optimizing the casting process and achieving the desired surface finish.
Improving Investment Casting Surface Finish: Post-Casting Processes
While careful control during the casting process is essential, post-casting processes play a vital role in achieving the desired surface finish:
1. Grinding and Machining: Refining Imperfections
Grinding and machining are common methods for removing surface imperfections, improving dimensional accuracy, and achieving a smoother finish. These processes can be used to correct minor flaws and achieve specific tolerances.
2. Shot Blasting and Tumbling: Surface Enhancement Techniques
Shot blasting and tumbling are surface treatment methods used to improve the surface finish and remove minor defects. Shot blasting uses abrasive media to remove surface irregularities, while tumbling employs abrasive media within a rotating barrel. These processes offer effective surface enhancement with minimal material removal.
3. Polishing and Buffing: Achieving a High-Gloss Finish
Polishing and buffing are used to achieve a highly polished, aesthetically pleasing surface finish. These techniques remove minute imperfections and create a smooth, reflective surface. This is particularly important for applications where appearance is critical.
Selecting the Right Surface Finish for Your Application
The ideal investment casting surface finish depends heavily on the application. Consider the following:
- Functionality: Some applications require a high-precision surface finish, while others are less demanding.
- Aesthetics: The desired appearance of the final product influences the level of surface finishing required.
- Cost: More advanced surface finishing techniques can increase the overall cost of the casting.
By carefully controlling the casting process and utilizing appropriate post-processing techniques, you can achieve the optimal surface finish for your specific needs. Remember, collaboration with your investment casting supplier is key to ensuring successful results. Their expertise can help you choose the appropriate processes and materials to achieve the desired quality and cost-effectiveness.
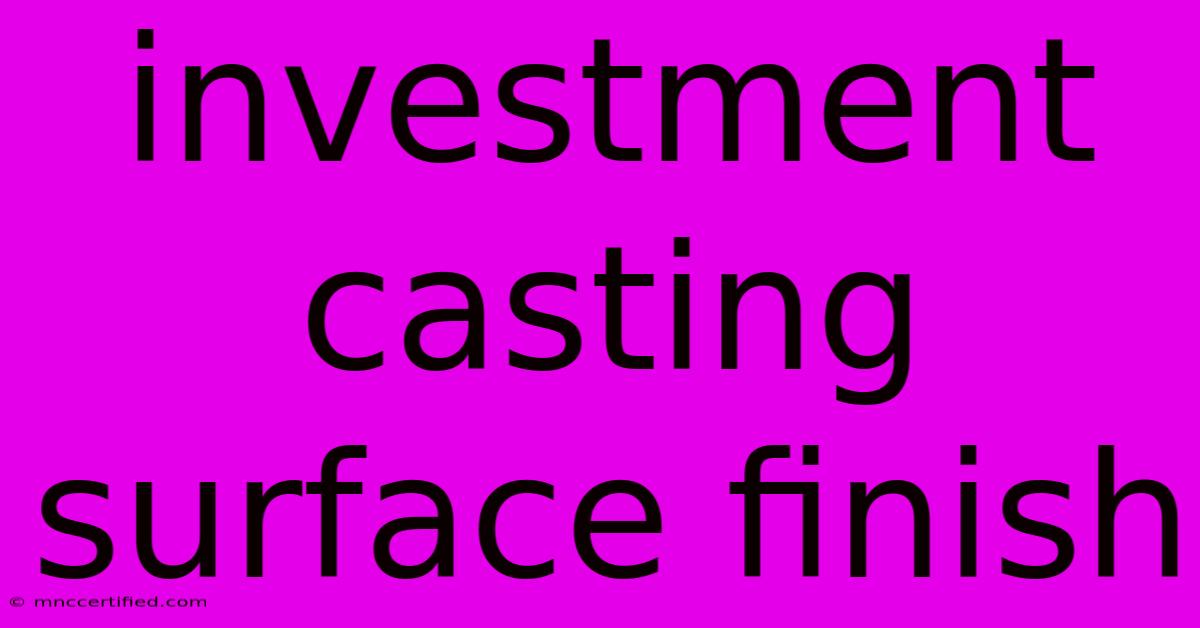
Thank you for visiting our website wich cover about Investment Casting Surface Finish. We hope the information provided has been useful to you. Feel free to contact us if you have any questions or need further assistance. See you next time and dont miss to bookmark.
Featured Posts
-
Stump Grinding Business Insurance
Nov 20, 2024
-
Paul Jogopulos Fisher Investments
Nov 20, 2024
-
Two Bears Trading Post Ruidoso Nm
Nov 20, 2024
-
Lakeside Trading Union Springs Ny
Nov 20, 2024
-
Two Bears Trading Post New Mexico
Nov 20, 2024