Investment Casting Vs Die Casting
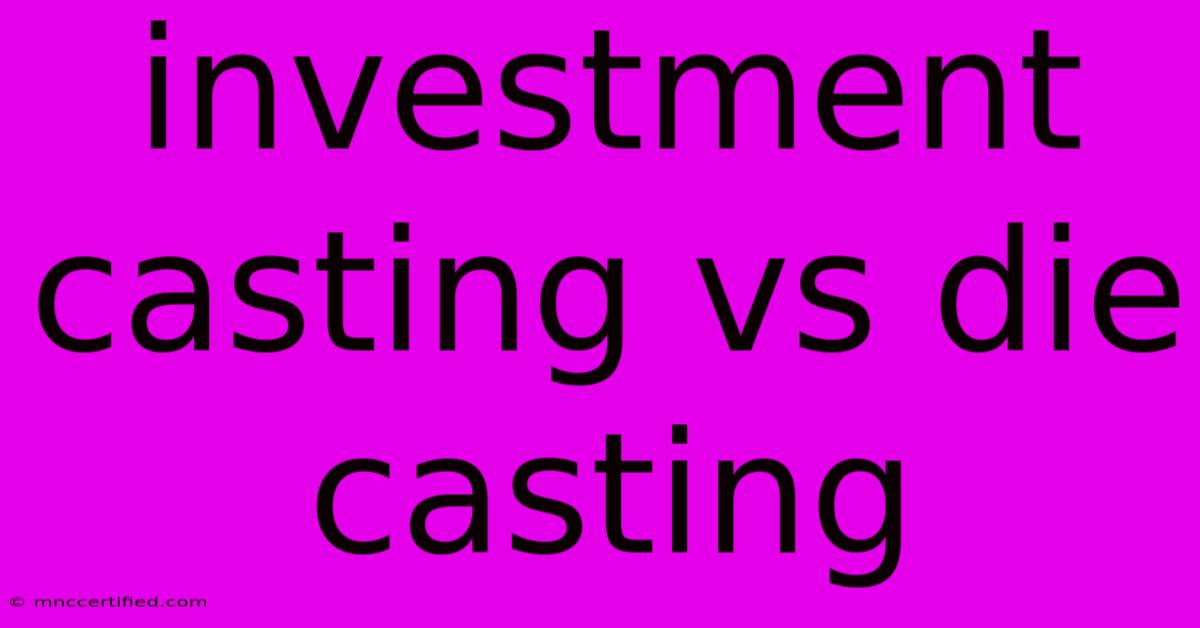
Table of Contents
Investment Casting vs. Die Casting: Which Process is Right for Your Project?
Choosing the right manufacturing process is crucial for the success of any project. When it comes to metal casting, two prominent contenders often top the list: investment casting (also known as lost-wax casting) and die casting. Both methods offer unique advantages and disadvantages, making the selection process critical. This comprehensive guide will delve into the intricacies of investment casting vs. die casting, helping you determine which process best suits your specific needs.
Understanding Investment Casting (Lost-Wax Casting)
Investment casting is a highly precise metal casting process known for its ability to produce intricate and complex parts with exceptional surface finish. This method involves creating a wax model of the desired part, which is then encased in a ceramic shell. The wax is melted out, leaving a cavity that's filled with molten metal. Once cooled and solidified, the ceramic shell is broken away, revealing the final metal casting.
Advantages of Investment Casting:
- High Precision and Detail: Investment casting excels in producing parts with intricate geometries, thin walls, and complex internal features, often exceeding the capabilities of other casting methods.
- Excellent Surface Finish: The process results in a smooth surface finish, often requiring minimal post-processing.
- Wide Range of Materials: Investment casting is compatible with a vast array of metals, including ferrous and non-ferrous alloys, such as steel, aluminum, and copper alloys.
- Near-Net Shape Capability: Minimal machining is often required, reducing overall production time and costs.
Disadvantages of Investment Casting:
- Higher Cost: Compared to die casting, investment casting is generally more expensive due to the intricate tooling and labor-intensive nature of the process.
- Lower Production Volume: While suitable for mass production, investment casting is less efficient for extremely high-volume applications compared to die casting.
- Longer Lead Times: The multi-step process contributes to longer lead times than die casting.
Understanding Die Casting
Die casting is a high-speed metal casting process that uses a reusable metal mold (die) to produce parts rapidly. Molten metal is injected under high pressure into the die, where it cools and solidifies. Once the part is ejected, the process is repeated.
Advantages of Die Casting:
- High Production Rates: Die casting is exceptionally efficient for mass production, offering significantly faster cycle times than investment casting.
- Cost-Effective for High Volumes: The reusable die makes it highly economical for large-scale production runs.
- Good Dimensional Accuracy: Die casting generally produces parts with acceptable dimensional accuracy, though not as precise as investment casting.
- Various Metal Options: While commonly used with zinc, aluminum, and magnesium, die casting can also accommodate other metals.
Disadvantages of Die Casting:
- Limited Design Complexity: Die casting is less suitable for parts with extremely intricate geometries or thin walls due to limitations in die design and metal flow.
- Surface Finish Limitations: The surface finish may require further processing, such as machining or polishing, to achieve the desired quality.
- Higher Tooling Costs: While cost-effective for high volumes, the initial tooling costs for die casting can be substantial.
- Potential for Porosity: Die casting can result in porosity, affecting the mechanical properties and requiring post-processing techniques to mitigate.
Investment Casting vs. Die Casting: A Direct Comparison
Feature | Investment Casting | Die Casting |
---|---|---|
Complexity | High | Moderate |
Precision | Very High | Good |
Surface Finish | Excellent | Good (often requires post-processing) |
Production Rate | Moderate | High |
Cost per Part | Higher | Lower (for high volumes) |
Tooling Cost | Lower | Higher |
Lead Time | Longer | Shorter |
Material Options | Wide range | Primarily zinc, aluminum, magnesium, etc. |
Choosing the Right Process
The choice between investment casting and die casting hinges on several factors, including:
- Part complexity: For intricate parts, investment casting is preferred.
- Production volume: High-volume production favors die casting.
- Budget: Consider the initial tooling costs and per-unit costs.
- Required surface finish: Investment casting typically offers a superior surface finish.
- Material requirements: Choose a process compatible with your chosen metal.
By carefully weighing these factors, you can make an informed decision and select the most suitable casting process for your specific project, optimizing cost, quality, and production efficiency. Consulting with experienced manufacturers is highly recommended to navigate these complexities.
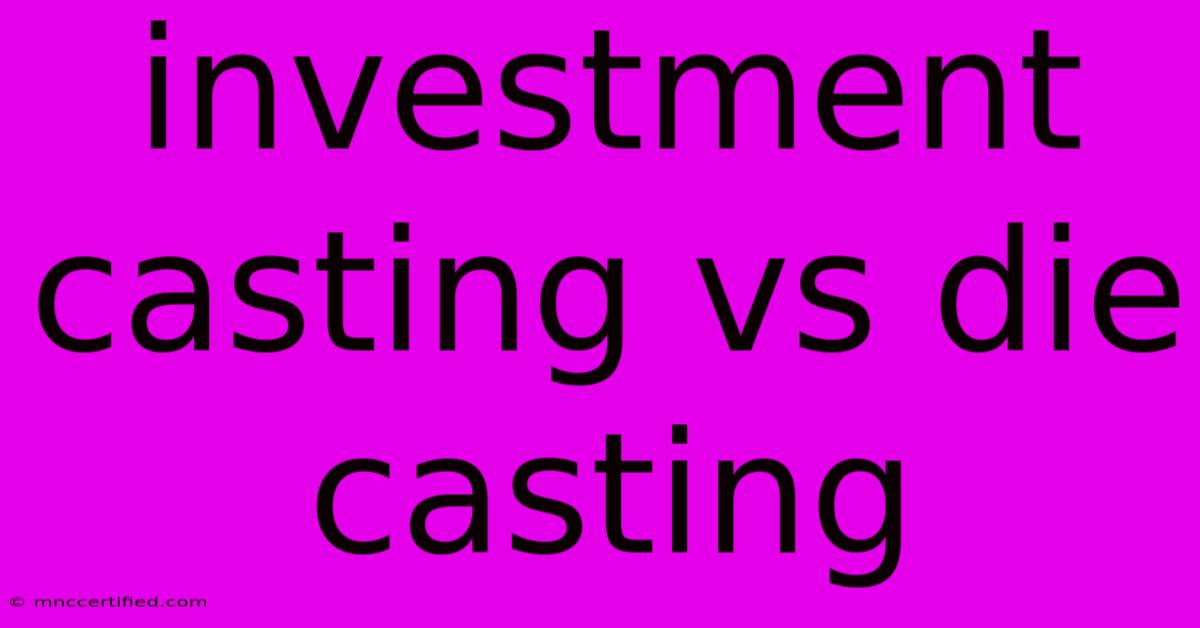
Thank you for visiting our website wich cover about Investment Casting Vs Die Casting. We hope the information provided has been useful to you. Feel free to contact us if you have any questions or need further assistance. See you next time and dont miss to bookmark.
Featured Posts
-
Best Breitling Watch To Invest In
Nov 20, 2024
-
Travel Insurance For Eu Residents
Nov 20, 2024
-
Paul Jogopulos Fisher Investments
Nov 20, 2024
-
Investment Returns Crossword Clue
Nov 20, 2024
-
Salishan Family Investment Center
Nov 20, 2024