Metal To Metal Bonding Glue
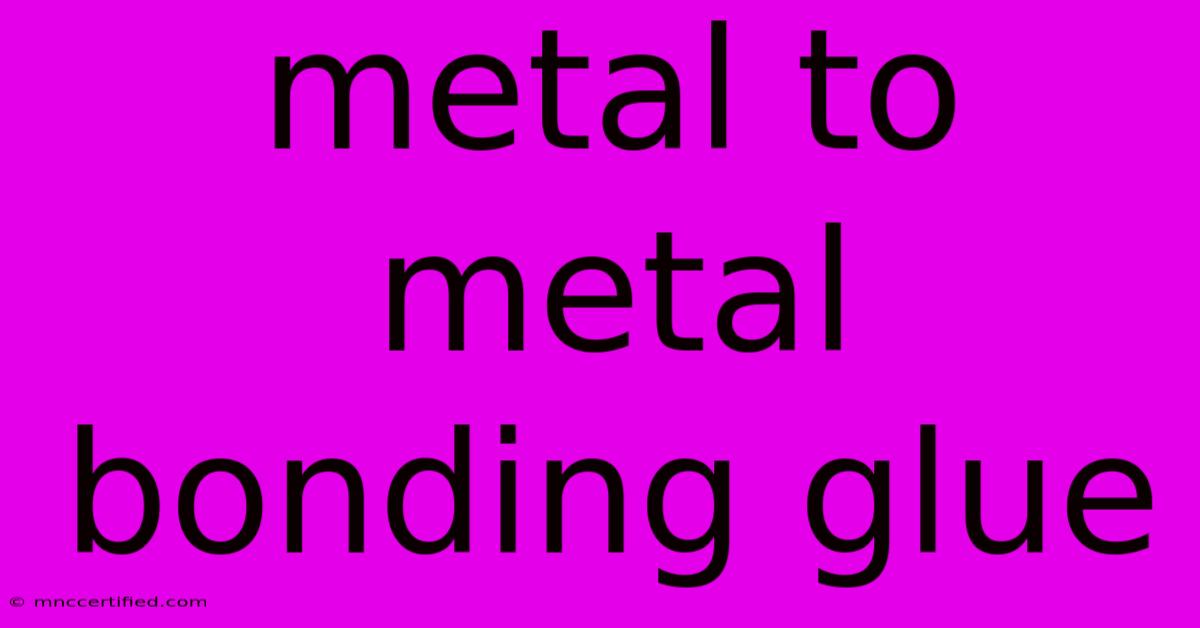
Table of Contents
Metal to Metal Bonding Glue: A Comprehensive Guide
Finding the right adhesive for metal-to-metal bonding can feel overwhelming. With so many options on the market, choosing the best glue for your specific needs requires careful consideration. This comprehensive guide explores the world of metal-to-metal bonding glue, helping you understand the different types, their applications, and crucial factors to consider before making your selection.
Understanding the Challenges of Metal-to-Metal Bonding
Metal surfaces are notoriously challenging to bond. Their inherent properties, such as smoothness, non-porosity, and potential for oxidation, often hinder adhesive adhesion. Successfully bonding metals requires an adhesive that can overcome these challenges and provide a strong, durable, and long-lasting bond. Factors such as the type of metal, the surface preparation, and the intended application significantly impact the choice of adhesive.
Key Challenges:
- Surface Preparation: Cleanliness is paramount. Oils, grease, oxides, and other contaminants can significantly weaken the bond. Proper surface preparation, often involving cleaning and roughening, is crucial.
- Thermal Stress: Metals expand and contract with temperature changes. The adhesive must be able to withstand these stresses without failing.
- Chemical Compatibility: The adhesive must be chemically compatible with both metals to ensure a strong and lasting bond. Different metals react differently with different adhesives.
- Strength Requirements: The bond strength needed varies depending on the application. Some applications demand extremely high shear and tensile strength.
Types of Metal to Metal Bonding Glue
Several types of adhesives excel at bonding metals. Each possesses unique properties making them suitable for specific applications.
1. Epoxy Adhesives:
- Strengths: Epoxy adhesives are versatile, offering good strength, chemical resistance, and temperature resistance. They are widely available and relatively easy to use. Many are specifically formulated for metal-to-metal bonding.
- Weaknesses: Curing time can be lengthy, and some require precise mixing ratios. They may not be suitable for high-temperature applications.
- Applications: General-purpose metal bonding, repairs, and structural applications where high strength isn't paramount.
2. Cyanoacrylate (Super Glue):
- Strengths: Cyanoacrylates offer fast curing times and good initial bond strength. They are easy to use and require minimal clamping.
- Weaknesses: They are generally less strong and less durable than epoxy adhesives, particularly in high-stress or high-temperature environments. They are also susceptible to moisture degradation.
- Applications: Quick repairs, small-scale bonding, and applications where fast curing is essential.
3. Acrylic Adhesives:
- Strengths: Acrylic adhesives offer a good balance between strength, flexibility, and ease of use. They are often suitable for a wider range of temperatures than cyanoacrylates.
- Weaknesses: May not be as strong as epoxy adhesives for high-stress applications.
- Applications: Bonding dissimilar metals, applications requiring some flexibility, and moderate-strength bonding.
4. Urethane Adhesives:
- Strengths: Urethane adhesives offer excellent toughness and flexibility, making them ideal for applications that experience vibration or shock.
- Weaknesses: Can have longer curing times than cyanoacrylates.
- Applications: Applications demanding high impact resistance and flexibility.
5. Anaerobic Adhesives:
- Strengths: These adhesives cure in the absence of air, creating a strong bond between tightly fitting metal parts. They offer excellent gap-filling capabilities.
- Weaknesses: Require a precise fit between the metal surfaces.
- Applications: Locking and sealing threaded components, preventing leaks, and bonding closely fitting parts.
Choosing the Right Metal to Metal Bonding Glue
The optimal glue for your project depends on several factors:
- Type of Metal: Different metals have different surface properties and chemical compositions, influencing adhesive compatibility.
- Application Requirements: Consider the required strength, temperature resistance, chemical resistance, and environmental conditions.
- Gap Size: Some adhesives are better suited for filling gaps than others.
- Curing Time: The required curing time will influence project scheduling.
- Cost: Adhesive costs vary considerably.
Surface Preparation: The Key to Success
Regardless of the chosen adhesive, proper surface preparation is crucial for a strong and lasting bond. This typically involves:
- Cleaning: Remove all oils, grease, dirt, and other contaminants using a suitable solvent.
- Roughening: Create a slightly rough surface to improve mechanical adhesion. Methods include abrading with sandpaper or using a chemical etching process.
- Priming: A primer can improve adhesion, especially on challenging surfaces.
Conclusion
Selecting the right metal-to-metal bonding glue is critical for achieving a strong, durable, and long-lasting bond. Understanding the various types of adhesives, their strengths and weaknesses, and the importance of proper surface preparation will guide you in making an informed decision for your specific project. Remember to always follow the manufacturer's instructions for optimal results. By carefully considering these factors, you can confidently tackle your metal bonding project and achieve the desired outcome.
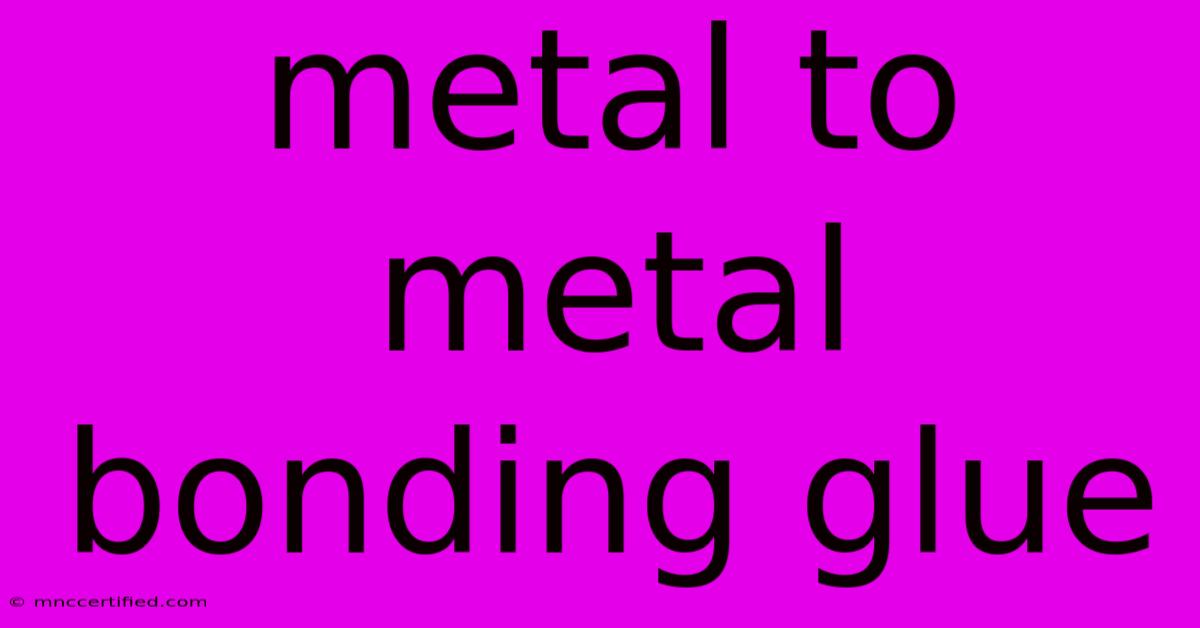
Thank you for visiting our website wich cover about Metal To Metal Bonding Glue. We hope the information provided has been useful to you. Feel free to contact us if you have any questions or need further assistance. See you next time and dont miss to bookmark.
Featured Posts
-
Libertadores Showdown Argentina Vs Brazil
Dec 01, 2024
-
Watch Dortmund Vs Bayern Free
Dec 01, 2024
-
New Driving Laws December 2024 Changes
Dec 01, 2024
-
Ndc Election Campaign Culminates December 5th
Dec 01, 2024
-
Barry Bonds 1987 Topps Card
Dec 01, 2024