Uv And Led Bonding Gels Are Used
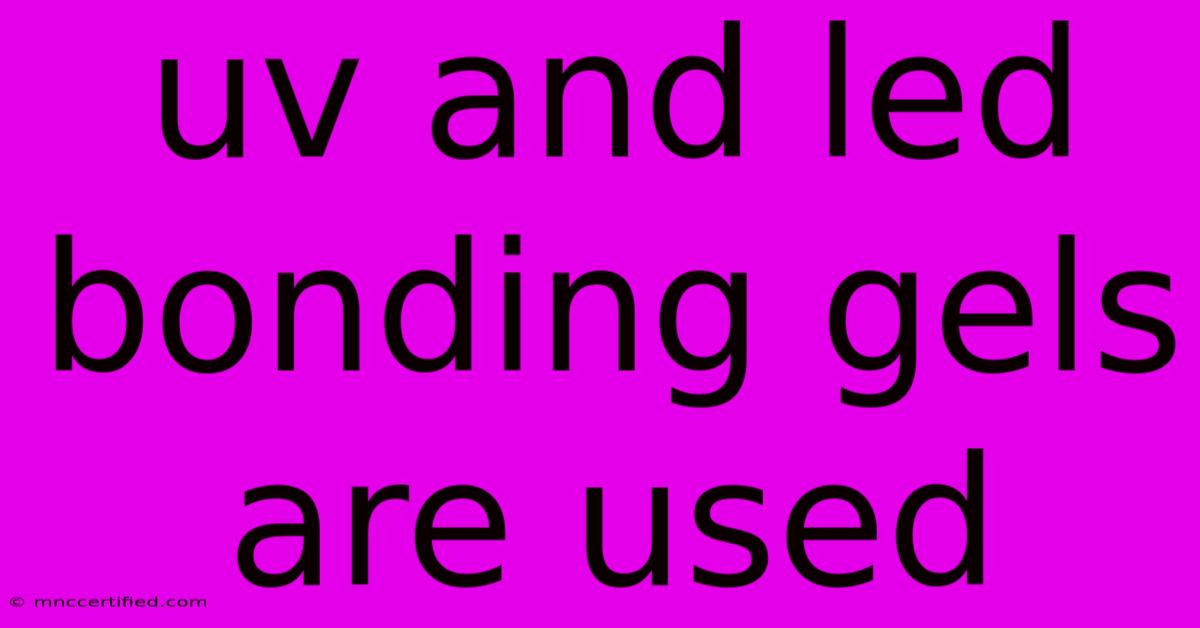
Table of Contents
UV and LED Bonding Gels: Uses and Applications
UV and LED bonding gels are revolutionizing various industries with their strong adhesive properties and ease of curing. Understanding their applications is key to leveraging their full potential. This article delves into the diverse uses of these powerful bonding agents, highlighting their advantages and considerations.
What are UV and LED Bonding Gels?
UV (ultraviolet) and LED (light-emitting diode) bonding gels are specialized adhesives that cure or harden when exposed to specific wavelengths of light. UV gels typically require exposure to a UV lamp, while LED gels cure under LED light sources. This curing process creates a strong, durable bond between various materials. The key difference lies in the curing speed; LED gels generally cure much faster than UV gels.
Key Advantages of Using UV/LED Bonding Gels:
- Fast Curing: LED gels offer significantly faster curing times compared to UV gels, boosting productivity.
- High Strength Bonds: These gels create incredibly strong and durable bonds, suitable for a wide range of applications.
- Precise Application: Their viscosity allows for precise application, minimizing waste and ensuring accurate placement.
- Versatility: They bond a variety of materials, including metals, plastics, glass, and ceramics.
- Clear and Color Options: Available in clear and various colors for both aesthetic and functional purposes.
- Low Shrinkage: Minimizes stress on bonded components during curing.
Diverse Applications of UV and LED Bonding Gels
The versatility of UV and LED bonding gels makes them suitable for a multitude of applications across numerous industries. Let's explore some key areas:
1. Industrial Manufacturing:
- Automotive: Bonding components in vehicles, such as sensors, lenses, and decorative trim. The speed and strength offered by LED gels are particularly valuable in high-volume automotive production.
- Electronics: Securing components on circuit boards, bonding delicate electronic parts, and encapsulating sensitive circuitry.
- Aerospace: Joining lightweight yet strong materials in aircraft and spacecraft construction, where durability and reliability are paramount.
- Medical Devices: Bonding components in medical devices, ensuring biocompatibility and a secure seal.
2. Optical Applications:
- Lens Assembly: Precisely bonding lenses in optical instruments, ensuring accurate alignment and light transmission.
- Fiber Optics: Connecting optical fibers, minimizing signal loss and ensuring reliable data transmission.
- Laser Systems: Securing optical components in laser systems, requiring high precision and stability.
3. Consumer Goods:
- Jewelry Making: Creating intricate settings and attaching gemstones. The clarity of clear gels enhances the brilliance of the stones.
- Craft and Hobby: Used in various craft projects requiring strong, durable bonds.
- Repair and Restoration: Repairing broken items, offering a strong and invisible fix.
4. Other Specialized Applications:
- Dental: Used in some dental procedures for bonding materials.
- Microelectronics: Bonding extremely small components in microelectronics manufacturing.
Choosing the Right UV/LED Bonding Gel
Selecting the appropriate gel depends on several factors:
- Materials to be bonded: The gel's compatibility with the materials is crucial.
- Required strength: The application dictates the necessary bond strength.
- Curing time: LED gels are ideal for faster production, while UV gels may be suitable for applications with less time pressure.
- Gap-filling properties: Some gels offer better gap-filling capabilities than others.
- Environmental conditions: Consider temperature and humidity.
Conclusion: The Future of Bonding
UV and LED bonding gels are more than just adhesives; they are crucial components in countless industries, enabling faster, more efficient, and stronger bonding solutions. Their versatility and continuous development promise exciting advancements in various sectors, solidifying their role in shaping the future of bonding technology. Understanding their applications and choosing the right gel is critical for harnessing their potential and optimizing production processes.
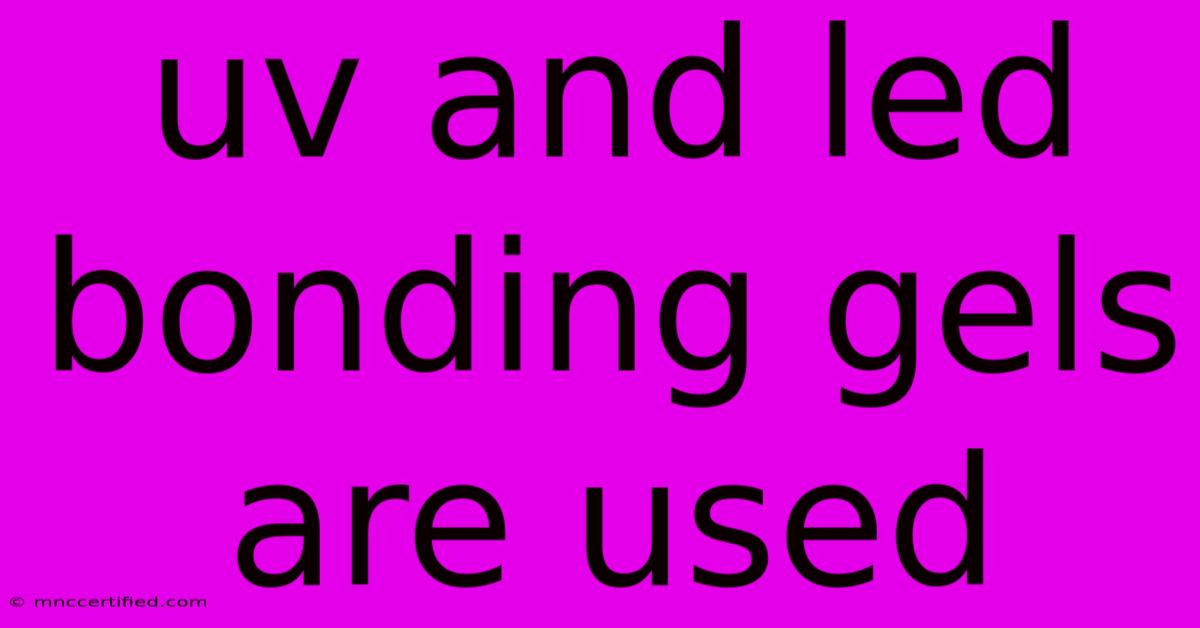
Thank you for visiting our website wich cover about Uv And Led Bonding Gels Are Used. We hope the information provided has been useful to you. Feel free to contact us if you have any questions or need further assistance. See you next time and dont miss to bookmark.
Featured Posts
-
Brazil Uruguay Score 1 1 Draw
Nov 20, 2024
-
Investar Bank Lafayette Louisiana
Nov 20, 2024
-
Treasure And Bond Leather Jacket
Nov 20, 2024
-
Ohio House Explosion 2 Dead 1 Injured
Nov 20, 2024
-
Epoxy Bonding Agent For Concrete
Nov 20, 2024