Vitrified Bond Grinding Wheel
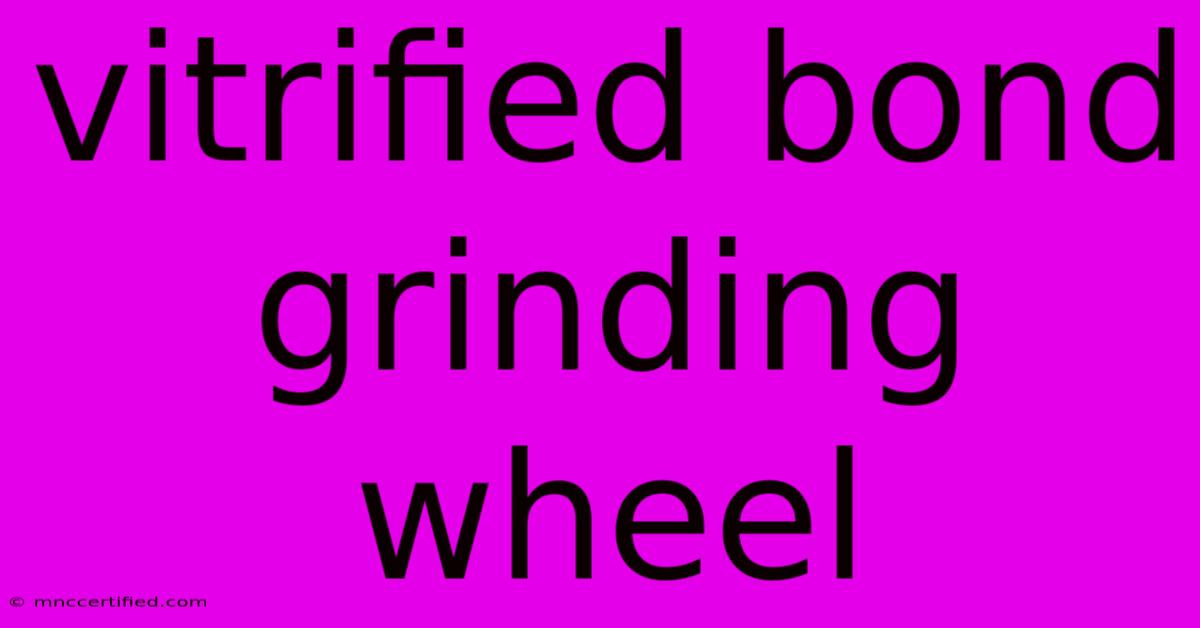
Table of Contents
Vitrified Bond Grinding Wheels: A Comprehensive Guide
Vitrified bond grinding wheels are a cornerstone of numerous industries, from precision machining to heavy-duty metalworking. Understanding their properties, applications, and selection is crucial for achieving optimal grinding performance and efficiency. This comprehensive guide delves into the specifics of vitrified bond grinding wheels, helping you choose the right wheel for your needs.
What are Vitrified Bond Grinding Wheels?
Vitrified bond grinding wheels are composed of abrasive grains (like aluminum oxide or silicon carbide) held together by a ceramic bond – a vitrified bond. This bond is formed by firing a mixture of abrasive grains and ceramic materials at high temperatures. The resulting wheel is characterized by its high strength, hardness, and resistance to wear. This makes them suitable for a wide array of grinding applications.
Key Advantages of Vitrified Bond Grinding Wheels:
- High Strength and Durability: Vitrified bond wheels are known for their exceptional strength, capable of withstanding significant forces during the grinding process. This leads to longer wheel life and reduced downtime.
- Precise Grinding: The hardness and uniformity of the vitrified bond allow for precise and accurate grinding, crucial for applications demanding high tolerances.
- High-Speed Performance: These wheels can operate at high speeds without fracturing, enabling faster material removal rates.
- Resistance to Thermal Shock: Their ability to withstand temperature fluctuations makes them ideal for applications involving significant heat generation.
- Clean Grinding: Vitrified bonds generally produce less glazing than other bond types, maintaining consistent cutting action throughout the wheel's life.
Disadvantages of Vitrified Bond Grinding Wheels:
- Brittleness: While strong, vitrified bond wheels can be brittle, making them susceptible to chipping or fracturing if mishandled or subjected to excessive shock.
- Difficult to Dress: Dressing (sharpening) vitrified bond wheels can be more challenging than other bond types due to the hardness of the bond. Specialized dressing tools and techniques are often required.
- Higher Initial Cost: Compared to some other types of grinding wheels, vitrified bond wheels tend to have a higher initial cost. However, their longer lifespan often offsets this initial investment.
Choosing the Right Vitrified Bond Grinding Wheel
Selecting the appropriate vitrified bond grinding wheel involves considering several factors:
1. Abrasive Type:
- Aluminum Oxide (Al₂O₃): Suitable for grinding steels, cast iron, and other ferrous metals. Offers good performance and economy.
- Silicon Carbide (SiC): Ideal for grinding non-ferrous metals, ceramics, stone, and other hard, brittle materials.
2. Grain Size:
Grain size dictates the wheel's aggressiveness. Coarser grains (larger numbers) are more aggressive, removing material faster, while finer grains (smaller numbers) are smoother, producing finer finishes.
3. Bond Hardness:
Bond hardness refers to the strength of the bond holding the abrasive grains. The harder the bond, the longer the wheel lasts but the slower the material removal rate. A softer bond wears faster but allows for quicker material removal. The correct hardness depends heavily on the application and material being ground.
4. Wheel Structure:
Wheel structure affects porosity. Open structures allow for better coolant penetration and chip clearance, improving grinding performance, especially on tougher materials.
5. Wheel Dimensions:
Wheel size and shape must match the application's requirements and machine specifications.
Applications of Vitrified Bond Grinding Wheels
Vitrified bond grinding wheels find extensive applications in various industries:
- Metalworking: Grinding and finishing of ferrous and non-ferrous metals.
- Tool and Die Making: Precise grinding of intricate shapes and high tolerances.
- Automotive Industry: Grinding of engine components, chassis parts, and other automotive components.
- Aerospace Industry: Grinding of high-performance materials with tight tolerances.
- Stone and Ceramic Industries: Grinding and shaping of stone and ceramic materials.
Safety Precautions When Using Vitrified Bond Grinding Wheels
Always prioritize safety when working with grinding wheels. This includes:
- Proper wheel mounting and balancing.
- Using appropriate safety guards and personal protective equipment (PPE), including eye protection and hearing protection.
- Following manufacturer's instructions carefully.
- Inspecting the wheel for cracks or damage before each use.
- Avoiding excessive speeds or pressure.
By understanding the properties, advantages, selection criteria, and safety precautions associated with vitrified bond grinding wheels, you can optimize your grinding processes for improved efficiency, precision, and safety. Remember to always consult the manufacturer's specifications and guidelines for optimal results.
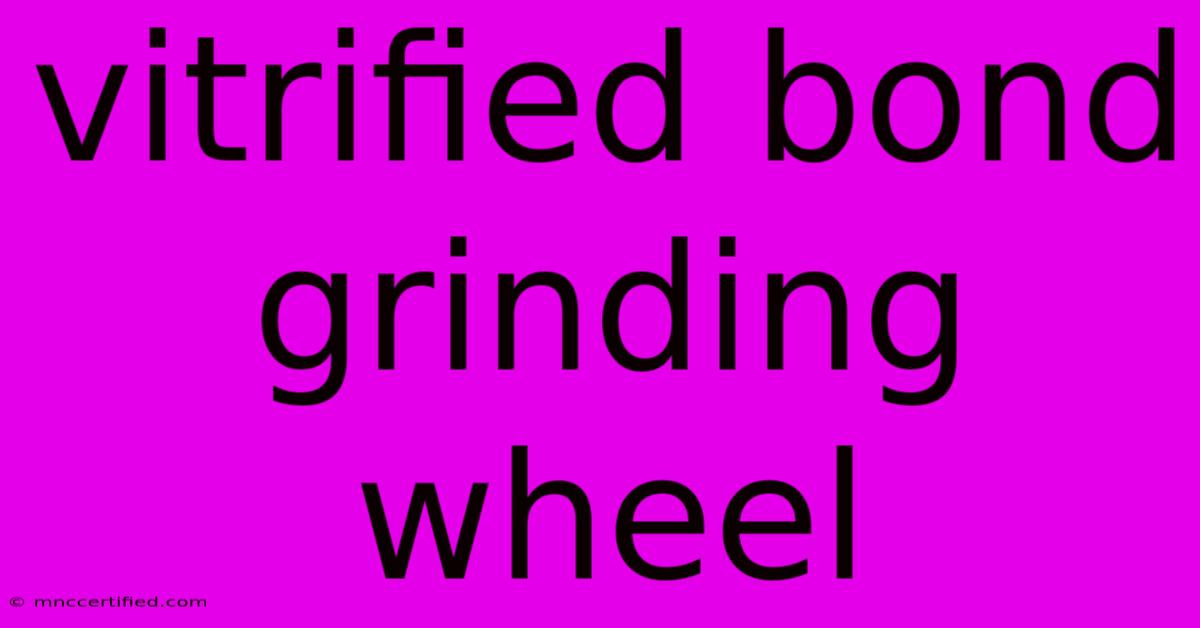
Thank you for visiting our website wich cover about Vitrified Bond Grinding Wheel. We hope the information provided has been useful to you. Feel free to contact us if you have any questions or need further assistance. See you next time and dont miss to bookmark.
Featured Posts
-
Kittery Trading Post Tent Sale
Nov 28, 2024
-
177m Euro Millions Win Uk Player
Nov 28, 2024
-
Stellantis Closes Uk Vauxhall Plant
Nov 28, 2024
-
England In Nz Bazball Tested
Nov 28, 2024
-
Unbroken Bonds 3 Pack Blister
Nov 28, 2024